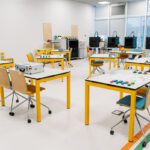
3 Powerful Ways to Use a Lean Manufacturing Game in Training
April 24, 2025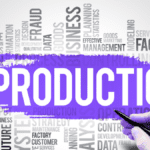
Operations Management Course: Your Path to Excellence in Business Processes
May 27, 2025Is your organization struggling with inefficiencies? Process improvement offers solutions to streamline workflows and boost productivity. This article examines five proven techniques that can help you reduce waste, enhance efficiency, and achieve better results.
Takeaways
- Process improvement enhances efficiency and effectiveness by assessing and refining your organization’s workflows to meet customer needs better.
- Methods such as Lean Manufacturing, Six Sigma, and Total Quality Management provide a framework for identifying inefficiencies and implementing changes.
- Having a continuous improvement mindset enables organizations to stay competitive, reduce costs, and enhance employee satisfaction through streamlined processes.
What is Process Improvement
Business process improvement is a method for enhancing the efficiency and effectiveness of an organization’s existing business processes. It involves continuous assessment and refinement to make processes faster and more cost-effective while adapting to changing customer needs. In a digital world, organizations must enhance their business processes to succeed and thrive. This means evaluating where improvements can be made in your processes and using structured methods to implement change.
The goal of process improvement is to meet customer needs and grow by optimizing workflows and core business processes. This means sustained growth and responsiveness to market changes. Process improvement can involve eliminating duplication, simplifying complex processes, utilizing new technology, or implementing automation. A key part of improving processes is creating a culture of continuous improvement where team input is valued, and suggestions are encouraged without fear of reprimand.
More transparency and alignment in process improvement clarifies roles and improves collaboration. Standardizing processes through guidelines reduces waste and ensures the delivery of high-quality services and products. Ultimately, process improvement means refining processes to get dramatic efficiency and cost savings.
Benefits of Process Improvement
Improved processes lead to higher employee productivity by eliminating repetitive tasks and streamlining workflows. This not only improves process efficiency but also empowers employees to focus on more value-added activities, ultimately enhancing overall productivity. Identifying and removing bottlenecks in workflows makes business better for organizations.
Cost reduction is a significant benefit of process improvement, allowing organizations to allocate resources more effectively. Eliminating inefficiencies will enable resources to be used more effectively, resulting in substantial cost savings. Additionally, improving processes leads to enhanced customer service and higher quality standards, while meeting deadlines results in increased customer satisfaction. Upgrading technology through process improvement also means higher customer satisfaction by getting quicker responses. Having a continuous improvement mindset as a core strategy means ongoing competitiveness and innovation for your organization. Improving processes means higher employee satisfaction by reducing the tedious tasks in their work. Overall, continuous improvement leads to significant improvements in service quality, efficiency, and customer satisfaction.
Process Improvement Methodologies
Different process improvement methodologies and other process improvement methods help organizations evaluate and adapt their processes for better profitability. Knowing multiple business process improvement methodologies is essential to finding the best fit for your organization. There are many methodologies available, each with its principles and tools to refine processes and achieve business objectives.
The Lean Manufacturing methodology focuses on eliminating waste and optimizing workflows to add value. Six Sigma uses data-driven techniques to minimize defects and variability in processes. Total Quality Management (TQM) is about achieving continuous improvement and customer satisfaction through the total involvement of all employees. Each of these methodologies has its advantages and can be tailored to your organization’s needs.
Lean Manufacturing
Lean methodology means creating more value with fewer resources by eliminating non-value-adding activities. Lean process improvement primarily focuses on eliminating waste. This focus helps to improve efficiency and productivity. Key principles are defining value and mapping the value stream. They also emphasize continuous flow, pull systems, and perfection.
Lean Manufacturing aims to eliminate waste and optimize processes, add value, and reduce costs. Expected outcomes include cost reduction and increased productivity. Implementing Lean yields additional benefits, including faster time to market, a better workplace culture, and improved customer relationships.
Lean Manufacturing tools, such as 5S, a workplace organization technique, improve productivity by standardizing processes. Kanban, a visual tool, manages tasks within a process, improving task management, transparency, and collaboration.
The Toyota Production System employs the Kaizen approach, which involves making continuous small positive changes.
Six Sigma
Six Sigma is a data-driven methodology that originated at Motorola, aiming to minimize variations and defects in processes. It aims for a defect rate of less than 3.4 defects per million opportunities, which means a highly optimized process. The two primary sub-methodologies employed in Six Sigma are the DMAIC process, which focuses on improving existing methods, and DMADV, which is used for developing new processes.
Lean Six Sigma is often integrated into these approaches to improve efficiency. Six Sigma relies on data-driven analysis of defects and root causes during the analysis stages, refining processes to achieve near-perfect outcomes, service quality, and customer satisfaction. The Sigma process is key to maintaining these standards.
Total Quality Management (TQM)
Total Quality Management (TQM) is a holistic management approach focused on continuous improvement and customer satisfaction that emerged in the late 1980s.
Key principles of TQM are:
- Strong customer focus
- Total employee involvement
- Process centered thinking
- Integrated systems
- Continuous improvement
The goal of implementing TQM is to improve processes and create long-term business success through customer satisfaction. TQM involves all employees in identifying improvements and making minor changes to processes.
This collective effort ensures that the entire organization is aligned to deliver high-quality products and services.
Process Improvement Techniques
Root cause analysis finds the underlying reasons for inefficiencies. Identifying and addressing root causes is key to reducing waste and business process outcomes. Tools like Ishikawa diagrams are used in process improvement for brainstorming potential causes of defects.
A thorough focus on root causes means an organization won’t get sidetracked by frameworks and jargon, keeping improvement efforts on track. By addressing the root causes, organizations can implement sustainable changes that lead to significant improvements in process performance.
Root Cause Analysis
Root cause analysis uncovers the fundamental reasons behind inefficiencies. Identifying and addressing root causes is vital for reducing waste and improving business process outcomes. Tools like Ishikawa diagrams are used in process improvement for brainstorming potential causes of defects.
A thorough focus on root causes can prevent an organization from being sidetracked by frameworks and terminologies, keeping improvement efforts aligned with goals. By addressing the root causes, organizations can implement sustainable changes that lead to significant improvements in process performance.
Value Stream Mapping
Value stream mapping is a visual tool to analyze and improve workflows. Its purpose is to document all steps involved in delivering a product and identify which activities add value and which don’t. A value stream flowchart shows each step to complete a process. It provides a visual representation of the whole process.
Highlighting non-value-added steps, value stream mapping helps to distinguish between value-added and non-value-added activities. This clarity enables organizations to streamline workflows, reduce waste, and improve overall efficiency.
5 Whys
The 5 Whys technique is used to find the root causes of problems. In a 5 Whys analysis, the question ‘Why?’ is asked 5 times to drill down to the root cause of the issue. This simple yet powerful technique helps organizations identify and address the underlying problems that hinder process performance.
Steps to Process Improvements
Business process improvement methods help implement lasting changes. Effective process improvement involves using specific frameworks. This helps to avoid common pitfalls during process optimization. A formal process improvement plan helps to establish accountability for improvement initiatives by defining objectives and timelines.
Identifying inefficiencies, bottlenecks, and waste is crucial to process analysis, enabling the improvement of workflows. Creating a detailed flowchart that shows steps, inputs, outputs, and stakeholders is essential for mapping out a current process.
Summarizing the steps involved in the entire organizational process improvement process provides a clear framework for organizations to enhance their processes.
Identify Areas for Improvement
Identifying areas for improvement aims to achieve process excellence and prepare for long-term success. Processes that are suitable for improvement typically have inefficiencies, are time-consuming, lack standards, and have bottlenecks. Determining the problem, such as a communication breakdown or workflow bottlenecks, is the first step in identifying process improvement needs.
Consulting with team members ensures that process management and improvement solutions are practical and relevant to their needs. A process improvement plan should include specific due dates, clear deliverables, defined roles, and established accountability.
Assessment tools can be used to evaluate existing workflows and identify areas for improvement through rapid application development.
Develop Improvement Strategies
Actionable improvement strategies should be based on thorough analysis and input from stakeholders. These strategies need to be specific, measurable, achievable, relevant, and time-bound to ensure they lead to practical process improvements.
Collaborating with team members ensures that the developed strategies are practical and aligned with the organization’s goals.
Implement Changes
Top-down support is crucial for the success of process improvement initiatives. A negative view of improvement can reduce buy-in from employees, making their involvement critical to the process. Training ensures understanding and sustainability of implemented improvements after changes. Collecting baseline data before implementing changes helps measure the impact of those improvements.
Effective communication ensures that improvements are understood and function correctly within the organization. Communicating potential disruptions and overall goals to those involved is vital during process improvements. Notifying all stakeholders about process changes ensures awareness and smooth adoption.
Ongoing monitoring is crucial to ensure the effectiveness and efficiency of a new workflow once it goes live.
Leveraging Technology for Process Improvement
Technology can enhance processes by providing real-time monitoring and analytics, thereby streamlining operations and ultimately improving efficiency. Automation can significantly reduce manual workloads, allowing employees to focus on more complex tasks. Standardizing recurring tasks and automating business processes reduces manual work, improving efficiency and accuracy.
Selecting the right process improvement technology involves considering budget, goals, and workplace culture. Evaluating emerging technologies continuously is essential for maintaining a competitive edge in process improvements. Leveraging technology effectively can lead to dramatic improvements in process performance and overall business transformation.
Continuous Process Improvement
Failing to adapt to changing environments can lead to the collapse of businesses. Continuous process improvement involves continuous improvement, which is critical for maintaining competitiveness and meeting customer expectations. Implementing continuous improvements enables companies to operate more efficiently and effectively, thereby saving time and resources. The goal of constant improvement is to optimize value and eliminate waste in processes, contributing to sustainable growth.
The PDCA cycle consists of four phases:
- Plan
- Do
- Check
- Act
It plays a crucial role in continuous process improvement. In the ‘Check’ stage, organizations evaluate outcomes against critical performance measures to ensure effectiveness. Regular data collection and performance tracking help assess the effectiveness of process improvements.
To stay effective, process improvements should be reviewed regularly, ideally every three to six months. Using flexible processes enables organizations to adapt to changes quickly.
Real-World Examples of Successful Process Improvements
Tata Steel improved its product quality and reduced rework time by adopting the Kaizen methodology. This incremental approach to continuous improvement enabled Tata Steel to consistently identify and rectify inefficiencies, resulting in significant improvements in product quality and a reduction in the time spent on rework.
Similarly, Collins Bus Corporation reduced downtime and improved resource efficiency by applying Lean techniques, showcasing the tangible benefits of this methodology. Mercedes-Benz Brazil achieved a 10-20% reduction in manufacturing hours per unit by implementing Lean and Kaizen practices, which were introduced at just the right time. These improvements not only enhanced production efficiency but also contributed to better resource management.
Vodafone improved its perfect purchase order rate from 73% to 85% through an enhanced process of mining, and 3M achieved annual savings of around $30 million through redesigning and reusing waste materials. These case studies provide valuable insights into the practical application of process improvement strategies across various industries, demonstrating the broad applicability and benefits of these methodologies.
Summary
In conclusion, process improvement is a vital strategy for organizations aiming to enhance efficiency, reduce costs, and stay competitive in a dynamic market. By understanding and implementing methodologies like Lean Manufacturing, Six Sigma, and TQM and utilizing techniques such as Root Cause Analysis, Value Stream Mapping, and the 5 Whys, businesses can achieve substantial improvements in their operations. The journey of continuous process improvement is ongoing, requiring regular evaluation and adaptation to ensure sustained growth and success. Embrace these strategies to transform your business processes and achieve a more efficient and prosperous future.
Frequently Asked Questions
What is the primary goal of business process improvement?
The primary goal of business process improvement is to enhance efficiency and effectiveness in organizational processes, ultimately making them faster and more cost-effective, thereby meeting the evolving demands of customers.
How does Lean Manufacturing improve business processes?
Lean Manufacturing significantly enhances business processes by eliminating waste and optimizing workflows, thereby increasing value, reducing costs, and improving productivity.
What are the key benefits of continuous process improvement?
Continuous process improvement significantly boosts productivity and reduces costs while also enhancing customer and employee satisfaction by streamlining operations and promoting innovation. Implementing these improvements can lead to substantial long-term gains for your organization.
How can technology enhance process improvement efforts?
The technology significantly enhances process improvement efforts by enabling real-time monitoring and analytics, which lead to more informed decision-making while also automating repetitive tasks to improve efficiency and accuracy.
What is the importance of the PDCA cycle in continuous improvement?
The PDCA cycle is crucial for continuous improvement as it provides a structured approach to defining goals, implementing changes, assessing results, and refining processes. This iterative feedback loop ensures sustained enhancements and organizational growth.
Key Takeaways
- Process improvement enhances efficiency and effectiveness by assessing and refining organizational workflows to meet customer demands.
- Key methodologies, such as Lean Manufacturing, Six Sigma, and Total Quality Management, provide structured frameworks for identifying inefficiencies and implementing changes.
- Adopting a continuous improvement mindset enables organizations to sustain competitiveness, reduce costs, and enhance employee satisfaction through streamlined processes.