Mastering the 5S Methodology: Essential Steps for Workplace Efficiency
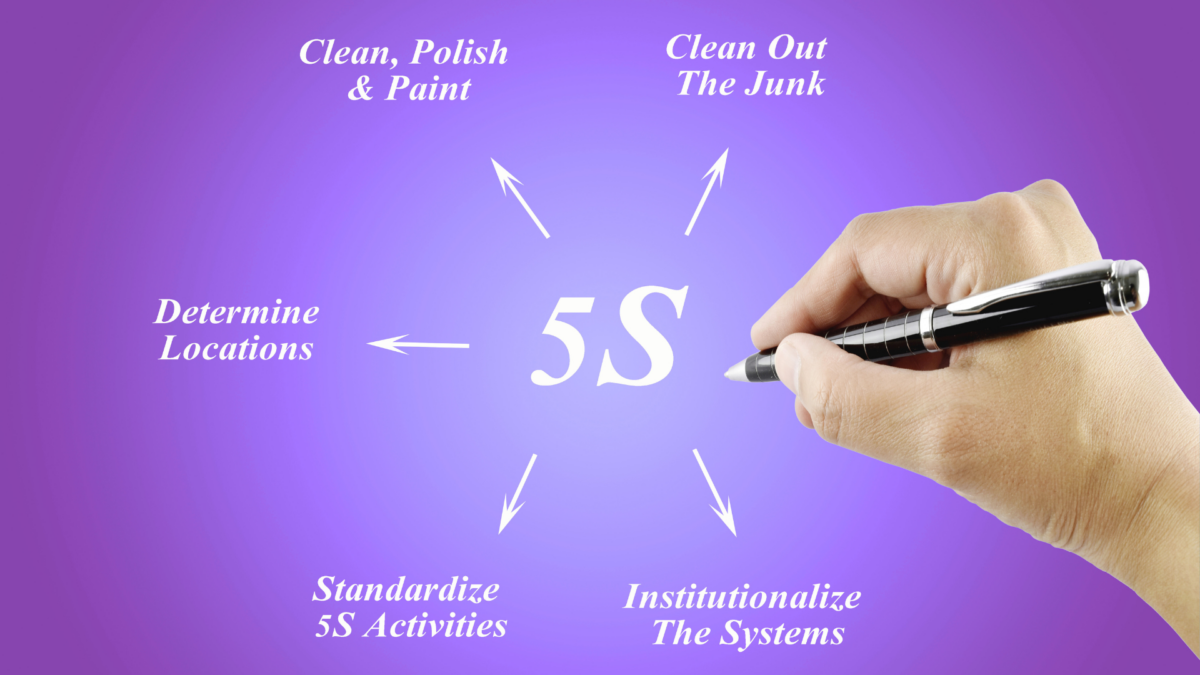
The 5S methodology is the foundation for continuous improvement — sustainable change is impossible without workplace organization.
The 5S methodology is a structured approach to organizing workplaces for better efficiency and reduced waste. It involves five steps: Sort, Set in Order, Shine, Standardize, and Sustain. The 5S methodology is based on the original Japanese words seiri, seiton, seiso, seiketsu, and shitsuke, translating to Sort, Set in Order, Shine, Standardize, and Sustain. This method helps create cleaner, more organized, and safer workspaces. In this article, we’ll explore each step and show you how 5S can boost productivity and safety in your workplace.
Key Takeaways
- The 5S methodology, originating from Toyota Motor Company, is a systematic approach to workplace organization that aims to improve efficiency and reduce waste.
- The core components of 5S include Sort, Set in Order, Shine, Standardize, and Sustain, each designed to enhance workplace organization and drive continuous improvement.
- Effective implementation of 5S requires careful planning, employee engagement, and ongoing audits to ensure sustained adherence and adaptation within different industries.
- Establishing and maintaining standard procedures is crucial for the sustainability of 5S practices, ensuring continuous maintenance and updates with active participation from managers and employees.
Understanding the 5S Methodology
The 5S methodology, a cornerstone of lean manufacturing, originated in Japan within the automotive industry, specifically the Toyota Motor Company. This systematic approach to workplace organization and production methods is crucial in enhancing agility in manufacturing and other sectors. Its focus on designated places for every item fosters a more organized and efficient workspace, embodying the principles of the Toyota production system and 5S lean.
While closely related to lean manufacturing and Six Sigma compliance, 5S is distinct in its focus and application. It is a foundation for more advanced lean production tools and processes, contributing significantly to continuous improvement initiatives. The ultimate goal of 5S is to enhance efficiency and organization, reduce waste, and improve overall productivity. The 5S methodology is widely applied in various manufacturing processes to enhance efficiency, organization, and quality control.
The Core Components of 5S
The 5S five-step methodology comprises five fundamental components: order, shine, standardize, sustain 1. Sort 2. Set in Order 3. Shine 4. Standardize 5. Sustain
Each of these steps plays a vital role in maintaining order and eliminating waste in the workplace.
Together, these steps form a comprehensive lean manufacturing system that improves workflow efficiency and supports Six Sigma compliance and continuous improvement. Here’s a closer look at each component and its contributions to workplace efficiency.
Sort
The Sort phase begins with assessing the workspace to identify and remove unnecessary items, enhancing efficiency and productivity. During this phase, a visual tagging system known as red tagging is employed to mark items of uncertain value for potential removal.
Items identified as unnecessary are moved to a ‘red tag’ holding area for further evaluation. If they remain unused after a set period, they should be permanently removed from the workspace. Reducing clutter and distractions allows employees to focus better on their tasks.
Set in Order
After removing unnecessary items, the Set in Order step organizes the remaining items for optimal workflow. Every item should have a designated location for easy access and return. This involves considering task frequency and workflow paths to arrange items logically.
Labels, floor markings, and shadow boards enhance clarity and maintain order. For example, placing a trash can under each cut station ensures that waste is disposed of efficiently, contributing to a cleaner and more organized workspace.
Shine
The Shine stage emphasizes cleaning the work area and performing regular maintenance to ensure tidiness. A clean environment allows issues like leaks and spills to be easily identified and addressed promptly, preventing more significant problems later.
Everyone takes responsibility for keeping their workplace clean, fostering a collective commitment to order. Regular cleaning and inspection promote a hygienic space and enhance efficiency by making it easier to identify misplaced items.
Standardize
Standardization involves systematizing cleaning and organization efforts into routines for consistency. Documenting repeatable processes helps maintain the first three steps of 5S. 5S checklists, schedules, and visual cues like signs and labels are essential tools in this phase of standardized work.
Standardization provides clarity, reducing the time spent explaining processes and enhancing efficiency. Maintaining compliance and ensuring long-term improvements are crucial to creating standards through a rigorous certification process.
Sustain
The Sustain step focuses on maintaining developed processes and continuous improvement. Embedding 5S practices into the organizational culture ensures ongoing adherence. Sustaining 5S requires self-discipline and commitment from everyone. Training new employees on 5S practices is crucial for maintaining the methodology and ensuring its long-term success.
Maintaining these practices over time improves process improvement, reduces waste, and enhances customer satisfaction.
Implementing 5S in Your Workplace
Implementing 5S in your workplace requires careful planning and commitment. Decide which departments and individuals will be involved to ensure practical contributions. Identify the necessary training and tools to facilitate implementation.
A clear timeline helps employees understand expectations during 5S implementation. Leadership commitment significantly influences employee engagement and adherence to new practices. Lack of company-wide commitment can significantly hinder successful 5S adoption. Understanding standard deviation is also vital for Six Sigma compliance, which complements the 5S methodology by minimizing defects and ensuring quality.
Employee Engagement
Employee engagement is vital for successful 5S implementation. Building employee buy-in can help mitigate resistance to new practices, and ongoing leadership support sustains implementation over time.
Practical 5S workshops and training programs actively involve all participants, with team leaders guiding sessions for alignment and motivation. Encouraging feedback allows 5S practices to adapt to changing business environments.
Visual Management Tools
Visual management tools are crucial in the 5S methodology. Shadow boards, infographics, and photographs enhance clarity and help maintain an uncluttered workspace in a visual workplace with visual controls.
Instructional videos and visual cues demonstrate where items belong, making it easier to maintain order. Involvement at all levels encourages active participation in 5S, ensuring everyone is on the same page.
Regular Audits and Reviews
Regular audits and reviews sustain 5S practices over time. Audits help maintain compliance, identify areas for improvement, and ensure continuous improvement.
Lean Strategies for Implementation
Implementing Lean strategies is crucial for organizations seeking to improve efficiency, reduce waste, and enhance customer satisfaction. One key component of Lean is the 5S methodology, which focuses on workplace organization and visual management. By applying the 5S principles of Sort, Set in Order, Shine, Standardize, and Sustain, organizations can eliminate waste, improve productivity, and create a more pleasant environment for employees.
The Toyota Production System (TPS) is a well-known example of a Lean manufacturing system that has successfully implemented 5S and other Lean strategies to significantly improve efficiency and quality. In manufacturing, 5S can reduce wasted time, improve workplace safety, and increase employee engagement. By incorporating 5S into their Lean strategies, organizations can create a culture of continuous improvement and achieve significant benefits, including improved efficiency, reduced waste, and enhanced customer satisfaction.
Best Practices for 5S
To ensure the successful implementation of 5S, organizations should follow best practices that promote employee buy-in, visual management, and continuous improvement. One key best practice is to start with a thorough Sort phase, removing unnecessary items and waste from the workplace. This helps create a clean and organized environment, making implementing the remaining 4S’s easier.
Another best practice is to use visual controls, such as signs and labels, to create a visual workplace that is easy to navigate and understand. Standardized work procedures and regular audits are also essential for maintaining order and ensuring that the 5S principles are followed. Additionally, organizations should encourage employee participation and feedback, providing training and recognition for employees who contribute to the 5S effort.
By following these best practices, organizations can create a sustainable 5S system that drives continuous improvement and achieves significant benefits, including improved efficiency, reduced waste, and enhanced customer satisfaction.
Benefits of 5S
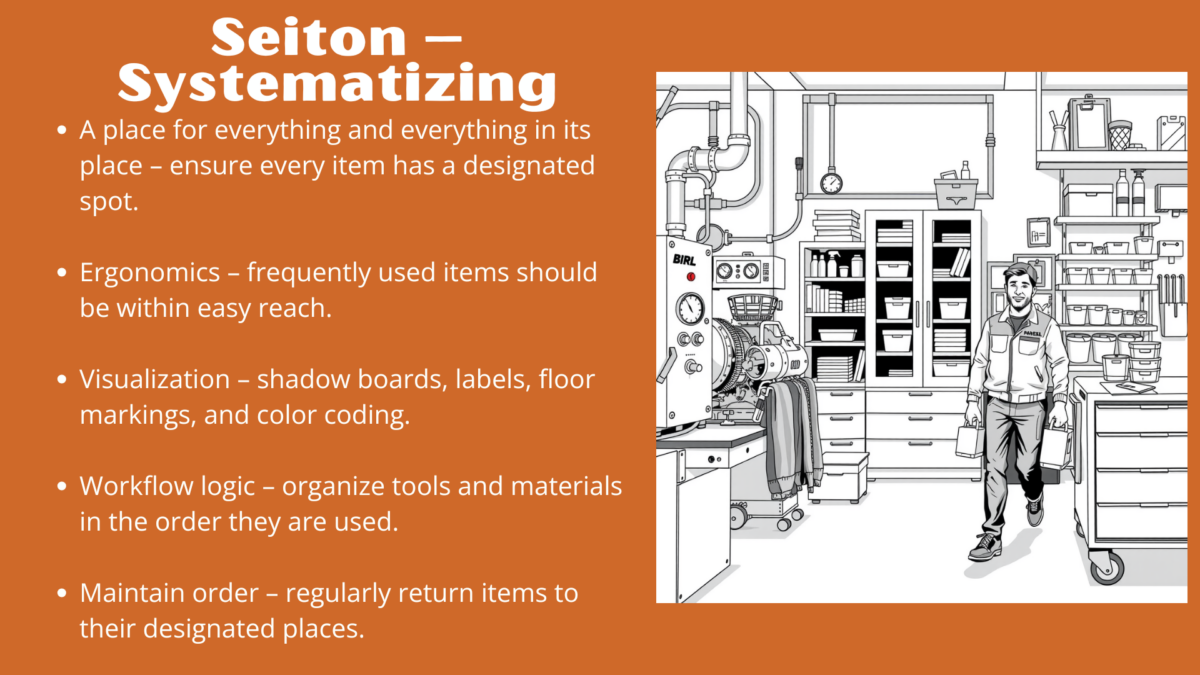
Seiton, the second step of the five S methodology, ensures everything has its place, forming the backbone of efficient and safe operations.
Systematic, common-sense application of 5S leads to improved operational efficiency, reduced time lost to disorganization, and enhanced workplace safety. It serves as a foundation for advanced lean methodologies, facilitating continuous improvement.
In addition to improving productivity, 5S cultivates a culture of ownership, increasing morale and engagement. This methodology saves businesses money over time, contributing to a substantial, long-term financial impact.
Waste Reduction
Identifying and reducing different forms of waste is a primary goal of 5S. The Sort phase identifies and removes unnecessary items, reducing clutter and distractions. The Set in Order step minimizes waste from excess motion, enhancing operational efficiency.
Optimizing old production processes within the 5S framework increases work output in less time and reduces operational costs. This process improves productivity and contributes to a cleaner, more organized workspace.
Improved Productivity
A well-organized workplace is crucial for improved productivity. Cluttered work areas lead to wasting time and reduced productivity. Ensuring that only necessary items are purchased and organized logically allows workers to work efficiently on their tasks.
The 5S methodology creates a pleasant work environment, enhancing employee engagement and satisfaction. This leads to higher productivity and better overall business performance.
Enhanced Safety
Implementing 5S enhances workplace safety. Tagging defective tools and reducing hazards minimizes accident risks. Increased organization reduces common safety hazards like slips, trips, and exposure to danger.
Regular cleaning and maintenance prevent heavy equipment malfunctions and contamination from dirt and debris. These practices improve safety, improve quality control, and reduce defects in production, primarily when performed according to the manufacturer’s specifications.
5S in Different Industries
The application of 5S transcends manufacturing, impacting sectors like service, education, and healthcare. This versatility makes 5S valuable for improving efficiency and organization in any work environment.
Whether deleting obsolete files in digital workspaces or maintaining orderliness in hospitality settings, 5S principles adapt to different industries. Here’s how 5S is applied in manufacturing, healthcare, and office settings.
Manufacturing Industry
In manufacturing, 5S is fundamental for lean production, minimizing waste, and improving workflow. Companies like Toyota and Hewlett-Packard have implemented 5S to increase efficiency and ensure high-quality products.
Organizing workplaces on the manufacturing floor and labeling key elements helps companies achieve maximum productivity and minimize errors. Better organization and waste reduction lead to fewer materials on-site, minimizing hazards and improving efficiency. This improves operational efficiency and contributes to a safer work environment.
Healthcare Sector
In healthcare, adopting 5S improves the organization of medical supplies, directly influencing patient care quality. Proper labeling and organization ensure healthcare professionals provide timely and efficient care, enhancing patient safety.
Office Settings
Implementing 5S in office environments fosters organization, significantly increasing employee efficiency. A well-organized office environment enhances productivity and satisfaction, contributing to better overall business operations.
Overcoming Challenges in 5S Implementation
Implementing 5S comes with challenges. Common obstacles include resistance to change and difficulty sustaining processes over time. Addressing these challenges requires a strategic approach and organizational commitment.
The sixth step in the 5S methodology focuses on eliminating risks in work processes. Some believe safety is an outcome of the other five S’s rather than a separate step, making integrating safety into each phase essential.
Resistance to Change
Employee reluctance to adapt to new processes is a significant barrier to successful 5S implementation. Effective change management strategies help employees transition and understand the importance of 5S.
A brief history of 5S and its benefits can mitigate resistance and foster a positive attitude towards change. Engaging employees and addressing their concerns can lead to smoother implementation.
Maintaining Consistency
Consistency is crucial for the long-term success of 5S. The methodology should become a continuous cycle, repeated at the end of each work phase for ongoing improvement. Standardizing processes and maintaining discipline are essential to keep 5S effective. Maintaining consistency in 5S practices requires establishing and adhering to standard procedures.
Embedding 5S into the culture ensures everyone understands its importance and adheres to established standards. This approach maintains order and promotes continuous improvement and efficiency.
Integrating New Ideas
Integrating new ideas keeps the 5S methodology relevant and effective in evolving business environments. Observing other companies’ 5S practices can provide inspiration and innovative solutions.
Encouraging innovation within 5S involves team brainstorming and being open to employee feedback. Adapting new ideas leads to 5S’s sustained effectiveness in enhancing workplace efficiency.
Resources for Learning 5S
Various resources are available for organizations to learn and implement 5S. Educational programs, books, articles, workshops, and webinars provide valuable insights and practical guidance. Continuous learning and training are essential for effectively applying the 5S methodology.
These resources cover each of the five principles of 5S and their advantages, facilitating a comprehensive understanding of the methodology. Let’s explore some of the key resources available for learning 5S.
Online Courses and Certifications
Online courses and certifications provide a flexible and accessible way to learn 5S. These programs often include classroom settings, DVDs, or hands-on activities to ensure a thorough understanding of each principle.
Employees participating in 5S activities must be trained to ensure proper application and familiarity with the principles. Websites offering training materials, certification, webinars, and assessment templates are valuable resources for achieving Six Sigma compliance and continuous improvement. Six Sigma aims for only 3.4 defective units in every million attempts, emphasizing the statistical foundation of this quality management methodology.
Books and Articles
Literature on 5S methodology provides essential knowledge for effectively implementing and sustaining its practices in the workplace. Books like ‘5S for Operators’ and ‘The Lean Six Sigma Pocket Toolbook’ are highly recommended for learning 5S principles and practices.
Workshops and Webinars
Workshops and webinars offer an interactive learning environment that enhances understanding of the 5S methodology. Participating in these sessions fosters collaboration, practical application, and sharing of best practices among attendees.
Summary
The 5S methodology is a powerful tool for achieving workplace efficiency and organization. By implementing the five steps of Sort, Set in Order, Shine, Standardize, and Sustain, organizations can significantly improve productivity, reduce waste, and enhance safety. Each step is crucial in maintaining order, eliminating waste, and fostering continuous improvement.
In conclusion, the benefits of 5S extend beyond the manufacturing industry, impacting various sectors and creating a more efficient and organized work environment. Embracing the 5S methodology can lead to a culture of continuous improvement, ultimately driving long-term success and customer satisfaction. Additionally, implementing 5S improves efficiency and organization and helps save time by preventing future delays and enhancing workflow. Start your 5S journey today and witness the transformation in your workplace.
Ready to move beyond theory and put the 5S methodology into action? The Fundamentals of 5S gives you practical tools developed from 25 years of Lean Manufacturing experience.
Below is an example of our course. It’s entirely online, available anytime, and includes lifetime access — perfect for building knowledge and training employees now and in the future.
Frequently Asked Questions
What is the 5S methodology?
The 5S methodology is a systematic approach to workplace organization that emphasizes Sort, Set in Order, Shine, Standardize, and Sustain, thereby enhancing efficiency and productivity. Organizations can create a more organized and effective work environment by implementing this methodology.
How does 5S relate to lean manufacturing and Six Sigma?
5S is integral to lean manufacturing. It fosters an organized and efficient work environment, facilitates the principles of Six Sigma, and supports continuous improvement initiatives.
What are the benefits of implementing 5S in the workplace?
Implementing 5S in the workplace leads to improved productivity, waste reduction, enhanced safety, better organization, and a positive long-term financial impact. These benefits contribute significantly to an efficient and effective working environment.
How can I implement 5S in my organization?
To successfully implement 5S in your organization, prioritize planning, engage employees, secure leadership commitment, provide training, utilize visual management tools, and conduct regular audits for continuous improvement. This structured approach will help foster a culture of efficiency and organization.
Where can I learn more about the 5S methodology?
You can explore the 5S methodology through various online courses, certifications, books, and articles, and by attending workshops and webinars for practical insights and guidance.