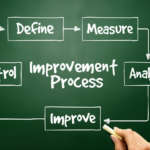
10 Best Techniques for Process Improvement in Manufacturing
April 23, 2025In the fast-paced world of manufacturing, efficiency is key to staying competitive.
We are always looking at production processes. We improve them to meet changing market needs.
One concept that has revolutionized these processes is SMED, or Single-Minute Exchange of Dies.
This method has changed how manufacturers handle changeovers. It is straightforward and reduces downtime while improving productivity.
But what exactly does SMED mean, and how can it help streamline your production process?
Let’s look at this important method closely. We will discover the main ideas and benefits that make SMED a key tool in lean manufacturing.
What are SMED Concepts?
SMED means Single-Minute Exchange of Dies. It is a method used in lean manufacturing. Its goal is to shorten the time needed to change from one production run to another.
In business, time is important. Being able to quickly switch between tasks can affect how much money a company makes.
The goal is to perform changeovers in less than 10 minutes, hence the term “single-minute”.
Shigeo Shingo, a Japanese industrial engineer, created this method. It is now an important part of lean manufacturing.
Many industries, like cars and electronics, use its principles. SMED is a common way to improve how things work better.
The SMED Meaning
SMED helps reduce the time machines are not working. This increases productivity.
By reducing changeover times, manufacturers can quickly adapt to changes in demand, produce smaller batches, and reduce inventory costs. In a competitive market, the agility to switch production quickly and efficiently is a significant advantage.
Being flexible is important in today’s market. Customer needs can change quickly, and businesses need to respond fast.
SMED helps make processes easier. This leads to better production that uses fewer resources and creates less waste.
The Core Concepts of SMED Lean
To truly understand SMED, it’s important to grasp its core concepts, which are designed to streamline the changeover process.
Each idea looks at different parts of the setup process. This ensures that someone checks each step for ways to make it better.
1. Internal vs. External Setup
A key idea of SMED is to split setup tasks into two groups: internal and external.
This differentiation is pivotal because it highlights where time savings can be most effectively achieved.
- Internal Setup: These are tasks that can only be performed when the machine is stopped. For example, removing a die from a machine is an internal task.
These tasks cause downtime and are the main target for reduction.
- External Setup: You can perform these tasks while the machine runs.
Getting tools or taking needed materials to the machine are examples of outside tasks.
- Manufacturers can maximize the machine’s productive time by identifying and optimizing these tasks.
The goal of SMED is to move more setup tasks from inside the machine to outside. This helps to reduce the time the machine is not working.
This change makes it faster to switch tasks. It helps staff use their time better, which improves overall productivity.
2. Streamline the Setup Process
Once tasks are categorized, the next step is to streamline the setup process.
This means you arrange tools, follow the same steps, and remove unnecessary steps.
By doing so, the setup process becomes more efficient and less prone to errors.
To streamline, you need to look closely at current practices.
This helps us find issues or steps that we can remove or simplify.
A good setup process helps make sure that all needed materials and information are ready. This can reduce the chance of problems or delays when switching tasks.
3. Continuous Improvement
SMED is not a one-time fix but a continuous process of improvement.
Regularly checking and improving the changeover process helps fix any new problems quickly.
The focus on getting better is why SMED is a useful tool in lean manufacturing.
Companies that use SMED well promote a culture of always getting better.
They encourage workers to find new ways to work better and faster.
This method keeps the benefits of SMED and encourages new ideas.
It makes the production process flexible and ready to change.
Implementing SMED in Your Production Process
Implementing SMED requires a systematic approach.
Here are the steps to use SMED in your production process. This will help you make changeovers more efficient.
Step 1: Observe and Analyze
The first step in using SMED is to watch how the current changeover process works.
This means closely observing how people perform changeovers now. The goal is to see each step and find ways to make it better.
Doing this can show how well the current method is working.
It helps set the stage for improvements in the future.
Document each step, noting how long each task takes and whether it is internal or external.
This analysis will help us make improvements.
Gather clear data to identify where you waste time and where changes will help the most.
This observation phase is important for understanding how things work now and finding areas that can be better.
Step 2: Identify and Separate Tasks
Look at the data you have. Find out which tasks happen inside the organization. These are the internal tasks.
Next, see which tasks involve people or groups outside the organization. These are the external tasks.
Look for opportunities to convert internal tasks to external ones. For example, if you need to gather tools after the machine stops, consider preparing them in advance.
This step usually needs creative thinking. Different departments might also need to work together to ensure they organize outside tasks well.
By moving tasks around, you can lower machine downtime and improve efficiency.
Step 3: Streamline and Standardize
Next, focus on streamlining the internal tasks that must remain. Standardize procedures to ensure consistency and efficiency. This might involve creating checklists, organizing tools, and training staff to follow the new procedures.
Standardization helps minimize differences. It ensures that every change meets the same high standard, regardless of who performs the job.
Being consistent is important for getting reliable results. This helps keep productivity high.
Step 4: Implement Changes and Train Staff
Once the new procedures are in place, implement the changes and train staff accordingly. Ensure that everyone involved in the changeover process understands the new procedures and the reasons behind them.
Good training is important for SMED. It helps employees do changeovers well and with confidence.
Understanding the benefits of SMED can help build a team.
This team can work on better quality and stay dedicated to their tasks.
Step 5: Monitor and Improve
Finally, monitor the new changeover process and gather feedback from the staff. Look for areas of further improvement and make adjustments as necessary. Remember, SMED is an ongoing process of refinement and optimization.
Regular feedback helps people learn and adapt. This makes sure the benefits of SMED last over time.
By staying alert and ready to adapt, you can make your production process efficient and innovative.
The Benefits of SMED
Using SMED can bring many benefits to your production process. It can change how your business works and competes in the market.
- Reduced Downtime: By minimizing changeover times, machines spend more time in production, increasing overall efficiency.
This increase in productivity leads to more work done and higher profits.
Increased Flexibility: Faster changeovers help manufacturers respond quickly to demand changes. This allows them to make smaller production batches and keep less inventory.
- This agility enables companies to offer more customized solutions and adapt swiftly to market trends.
- Cost Savings: Reduced inventory and improved efficiency lead to cost savings, enhancing the bottom line.
By using resources wisely and reducing waste, companies can save money and help meet sustainability goals.
Better Quality: Set procedures lower the chance of mistakes during changes, which helps make better products.
- Consistency in production processes ensures that each product meets the same high standards, enhancing customer satisfaction and brand reputation.
Real-World Examples of SMED
Many companies have used SMED to make their production better.
A famous car maker reduced their changeover times by over 50% using SMED methods.
This not only helped them make more products but also let them offer more models and deliver them faster.
Similarly, in the electronics industry, companies have leveraged SMED to accelerate product launches and respond rapidly to technological advancements.
These real-world examples show how helpful SMED is in many industries.
It can change how production works and help businesses gain an edge over others.
Conclusion
SMED is an important tool in lean manufacturing. It helps make the production process faster and more efficient.
By focusing on reducing changeover times, manufacturers can achieve greater efficiency, flexibility, and cost savings.
If you are new to lean manufacturing or want to make your processes better, SMED is a method to help you improve.
By staying focused and following a clear plan, anyone can benefit from SMED in any production environment.
Embrace SMED to keep your production process lean and competitive in today’s dynamic market.