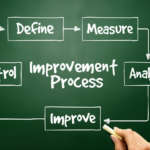
10 Best Techniques for Process Improvement in Manufacturing
April 23, 2025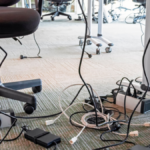
Effective Training on 5S to Boost Productivity
April 24, 2025Mastering Lean Productivity: Tips to Boost Efficiency and Save Time
Lean productivity aims to eliminate waste and boost efficiency in your operations. This article outlines the core principles, practical techniques, and real-world benefits of adopting lean strategies.
Key Takeaways
- Lean productivity focuses on eliminating waste, enhancing value creation, and promoting continuous improvement to optimize manufacturing processes.
- Key tools and techniques such as Just-in-Time (JIT), Value Stream Mapping, and Total Productive Maintenance (TPM) are essential for implementing lean practices effectively.
- Technology, including data-driven techniques and automation, plays a crucial role in enhancing lean manufacturing efficiency and supporting continuous improvement initiatives.
Understanding Lean Productivity
Lean manufacturing focuses on eliminating non-value-adding activities, promoting continuous waste elimination, and maximizing customer value. At its core, lean production is about optimizing production processes to achieve operational excellence, ensuring a smooth flow of products with minimal interruptions and delays. This holistic approach, often associated with the Toyota Production System, emphasizes efficiency and responsiveness, making it a powerful strategy for improving overall productivity.
Implementing lean manufacturing techniques involves a shift in mindset, fostering a culture of continuous improvement among all employees within a lean manufacturing system. Lean practitioners prioritize operational efficiency and strive to align their efforts with long-term strategic goals, guided by their management philosophy and lean thinking.
Core principles, such as value creation, waste elimination, and continuous improvement, drive lean manufacturing principles to produce higher-quality products, reduce costs, and enhance customer satisfaction.
Key Principles of Lean Productivity
The foundation of lean productivity lies in its core principles: value creation, continuous improvement, and eliminating waste. These principles guide every aspect of lean manufacturing, driving efforts to optimize processes, improve efficiency, and deliver higher-quality products.
Organizations aiming to implement lean production systems and achieve operational excellence must understand and embrace these principles.
Value Creation
Value creation is the cornerstone of lean manufacturing. Defining customer value from the customer’s perspective as the foundation for all operational decisions enables businesses to prioritize actions that enhance product quality and meet customer demands. This focus on customer satisfaction not only leads to higher-quality products but also results in significant cost savings and a competitive market advantage.
Continuous Improvement
Continuous improvement, a key principle of lean manufacturing, involves regularly assessing processes and implementing incremental enhancements in a constant process. Toyota’s implementation of the Toyota Production System, which emphasizes continuous improvement and waste reduction, serves as a model for other manufacturers.
Establishing key performance indicators (KPIs) and tracking efficiency helps organizations identify areas for ongoing improvement and drive operational excellence.
Eliminating Waste
Eliminating waste is crucial for improving efficiency and product quality in lean manufacturing. Identifying waste and reducing waste encompasses various types, including overproduction, idle time, and defects, all of which use resources ineffectively without delivering value.
Tools like Kaizen, Kanban, and Value Stream Mapping help identify and eliminate waste, ensuring a streamlined and efficient production process.
Implementing Lean Productivity Techniques
Implementing lean productivity techniques involves practical steps to identify and eliminate waste, enhance operational efficiency, optimize processes, and improve product quality. Techniques such as Just-in-Time (JIT), the Pull System, and Value Stream Mapping are essential for achieving these goals.
By focusing on these methods, organizations can create a lean production system that aligns with customer demands and drives continuous improvement.
Just-in-Time (JIT)
Just-in-Time (JIT) is a cornerstone of the Toyota Production System, emphasizing the production of goods only as needed to minimize inventory management and waste. By aligning production closely with actual customer demand, JIT reduces excess inventory and enhances operational efficiency.
This approach not only improves quality but also contributes to delivering higher-quality products and enhances customer responsiveness, resulting in improved quality.
Pull System
The Pull System, another key technique in lean manufacturing, focuses on producing items based on actual customer demand. This method minimizes waste by ensuring that products are made only when needed, reducing overproduction and aligning manufacturing output with customer requirements.
Value Stream Mapping
Value Stream Mapping is a powerful tool for visualizing and optimizing production processes. Creating flow throughout the entire production process enables organizations to identify inefficiencies, address bottlenecks, and streamline operations, ultimately enhancing process capability.
This visual tool provides a roadmap for continuous improvement and continuous flow, leading to increased efficiency and productivity.
Lean Tools for Enhancing Productivity
A variety of lean tools exist to enhance productivity and refine manufacturing processes. These lean manufacturing tools, including Total Productive Maintenance (TPM), Minute Exchange of Die (SMED), and Root Cause Analysis, have been successfully adopted by various companies across different sectors to achieve significant improvements in operational efficiency.
Effectively implementing lean methods requires a deep understanding and utilization of these tools.
Total Productive Maintenance (TPM)
Total Productive Maintenance (TPM) takes a proactive approach to maintenance. Its goal is to maximize the operational time and effectiveness of equipment. Involving all levels of staff in TPM increases uptime, reduces cycle times, and eliminates defects, which contributes to overall equipment effectiveness (OEE) and operational excellence.
Minute Exchange of Die (SMED)
SMED (Single Minute Exchange of Die) is a set of techniques designed to reduce setup times in manufacturing, enabling quicker transitions between different production tasks. Implementing SMED enables manufacturers to achieve greater flexibility and responsiveness, thereby enhancing efficiency and production agility.
Root Cause Analysis
Root Cause Analysis focuses on identifying and addressing deep-seated problems in production processes to formulate effective long-term solutions. Understanding the root causes of issues enables organizations to implement targeted improvements that boost overall efficiency and product quality.
The Role of Technology in Lean Productivity
Technology plays a crucial role in enhancing lean productivity by providing real-time insights, optimizing processes, and supporting continuous improvement. The integration of IoT, AI, and data analytics revolutionizes lean practices, enabling organizations to achieve operational excellence and remain competitive in a rapidly evolving market.
Data-Driven Techniques
Data-driven techniques, such as data analytics and IoT integration, significantly enhance decision-making and operational efficiency in lean manufacturing. Real-time monitoring and data collection through these technologies help identify inefficiencies and improve process capabilities.
Automation in Lean Manufacturing
Automation in lean manufacturing focuses on effectively applying technology to improve efficiency and reduce waste. However, it’s essential to apply automation thoughtfully to avoid complicating operations, ensuring that it enhances rather than hinders lean processes.
Digital Transformation
Digital transformation integrates emerging technologies, such as IoT and AI, to revolutionize lean manufacturing processes. Embracing digital transformation allows organizations to achieve continuous improvement, optimize processes, and enhance overall productivity.
Benefits of Lean Productivity
The benefits of lean productivity are manifold, including significant cost savings, improved product quality, and enhanced customer satisfaction. Companies that adopt lean productivity techniques report substantial reductions in operational costs, increased efficiency, and a quicker response to market changes, highlighting the key benefits of this approach.
Additionally, efficient supply chain management, utilizing lean strategies, enhances overall equipment effectiveness and streamlines operations.
Challenges and Solutions in Lean Productivity
Implementing lean productivity is not without its challenges. Common issues include resistance to change, inadequate employee training, and poor communication. Addressing these challenges is crucial for the successful adoption of lean practices and achieving operational excellence.
Overcoming Resistance to Change
Overcoming resistance to change requires building a strong culture centered on lean principles and lean practices while actively involving employees in the change process.
Training and ongoing support can alleviate fears and boost employee confidence in new processes.
Addressing Poor Communication
Effective communication is vital for the successful implementation of lean practices. Establishing regular planning meetings, open communication channels, and celebrating small wins can enhance team alignment and morale.
Case Studies of Successful Lean Productivity
Real-world case studies provide valuable insights into the practical applications of lean productivity principles. Various companies across different sectors have successfully applied lean management principles to address significant business challenges and drive operational efficiency.
Automotive Industry
Toyota’s implementation of the Toyota Production System has set benchmarks for efficiency and product quality in the automotive industry by emphasizing value creation, waste reduction, and continuous improvement.
Discrete Manufacturing
In the discrete manufacturing operations sector, lean principles have led to significant enhancements in operational efficiency and flexibility. By streamlining production processes and reducing cycle times, companies can respond more swiftly to market demands and deliver higher-quality products.
Supply Chain Optimization
Lean strategies in supply chain management focus on improving overall equipment effectiveness and minimizing waste throughout the supply chain. By adopting lean practices, organizations can enhance efficiency, reduce inventory costs, and better meet customer demands.
Summary
The journey through lean productivity reveals a comprehensive framework designed to optimize production processes, eliminate waste, and enhance efficiency. By embracing key principles such as value creation, continuous improvement, and waste elimination, organizations can deliver higher-quality products while reducing costs. Techniques such as Just-in-Time, Pull Systems, and Value Stream Mapping, supported by tools like TPM, SMED, and Root Cause Analysis, provide practical methods for implementing lean strategies effectively.
The integration of technology, including data-driven techniques, automation, and digital transformation, further enhances lean productivity by providing real-time insights and optimizing processes. Despite the challenges associated with lean implementation, such as resistance to change and poor communication, solutions exist to foster a strong lean culture and ensure successful adoption. Real-world case studies from the automotive and discrete manufacturing sectors, as well as supply chain optimization, illustrate the transformative power of lean productivity. By mastering these techniques, organizations can achieve operational excellence, remain competitive, and continually improve to meet the evolving demands of their customers.
Frequently Asked Questions
What is the primary goal of lean manufacturing?
The primary objective of lean manufacturing is to eliminate non-value-adding activities and maximize customer value while striving for continuous improvement and waste reduction. This approach leads to enhanced operational efficiency and effectiveness.
How does Just-in-Time (JIT) help in lean manufacturing?
Just-in-Time (JIT) enhances lean manufacturing by producing goods only as needed, which minimizes inventory and waste while aligning production closely with actual customer demand. This approach ultimately streamlines operations and increases efficiency.
What are the key benefits of implementing lean productivity techniques?
Implementing lean productivity techniques results in significant cost savings, improved product quality, and enhanced customer satisfaction, ultimately increasing operational efficiency and enabling a quicker response to market changes. These benefits collectively drive sustainable business growth and competitiveness.
What challenges might organizations face when implementing lean productivity?
Organizations often face resistance to change, inadequate employee training, and poor communication when implementing lean productivity. To overcome these challenges, it is essential to foster a strong lean culture and actively involve employees in the transition process.
How does digital transformation support lean manufacturing?
Digital transformation supports lean manufacturing by integrating technologies like IoT and AI, which enhance continuous improvement and optimize processes through real-time insights. This leads to better decision-making and increased efficiency in manufacturing operations.