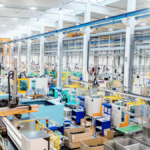
Lean Productivity Tips to Work Smarter and Faster
April 23, 2025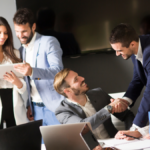
Teamwork Trainings to Strengthen Workplace Bonds
April 24, 2025Top Training on 5S: Mastering Lean Principles for Efficiency
Looking to improve your workplace efficiency with training on 5S? This article covers the core principles of the 5S methodology, its significant benefits, and practical tips for successful implementation.
Key Takeaways
- The 5S methodology comprises five steps: Sort, Set in Order, Shine, Standardize, and Sustain, focusing on improving workplace organization and efficiency.
- Developed in Japan as part of the Toyota Production System, 5S has been widely adopted globally as a fundamental lean manufacturing practice, enhancing productivity and quality.
- Effective 5S training emphasizes interactive learning, continuous education, and practical resources, leading to sustained improvements in operational efficiency and employee morale.
Understanding the 5S Methodology
At the heart of lean manufacturing lies the 5S methodology, a systematic approach to workplace organization that aims to improve efficiency and enhance productivity.
The 5S system comprises five key components:
- Sort
- Set in Order
- Shine
- Standardize
- Sustain
Each step builds upon the previous one, creating a cohesive framework for maintaining an orderly and effective work environment.
The first step, Sort, involves critically evaluating the items in your workplace and separating what is necessary from what is not. This step often employs a red tag system to identify problems and move items that are no longer needed to a holding area. Eliminating unnecessary clutter creates a more streamlined and manageable workspace.
Next comes Set in Order, where the focus shifts to organizing the necessary items for optimal efficiency. This involves developing storage solutions that are both logical and accessible, such as labeling and arranging tools and materials in a way that minimizes search time. Maintaining a smooth workflow and preventing disruptions hinges on effective organization.
Shine emphasizes the importance of cleanliness in the workplace. Regular cleaning routines not only maintain a pleasant work environment but also help identify potential equipment malfunctions before they become major issues. A clean workspace can reduce stress, reduces the risk of accidents, and ensures everything operates smoothly.
Standardize is the fourth step in the 5S methodology, ensuring that the practices established in the first three steps are consistently followed. This involves creating standard operating procedures that everyone adheres to, maintaining the improvements achieved. Standardization sustains the gains made and prevents a regression to old habits.
Finally, Sustain involves embedding these practices into the workplace culture, continually applying the 5S principles. This step is vital for long-term success, fostering a culture of continuous improvement and operational excellence.
The Origins and Evolution of 5S
The 5S methodology was born in Japan, deeply intertwined with the Toyota Production System, which revolutionized manufacturing processes worldwide. Taiichi Ohno, a key figure at Toyota, played a pivotal role in creating and refining this systematic approach alongside Shigeo Shingo. Together, they laid the foundations for what would become a cornerstone of lean manufacturing.
Initially developed to enhance the efficiency of Toyota’s production lines, the 5S system quickly proved its value, leading to significant improvements in productivity and quality. Shingo’s contributions were instrumental in educating Toyota engineers on the implementation of 5S, ensuring that the principles were deeply embedded in the company’s culture.
As word of Toyota’s success spread, Western manufacturing organizations began to take notice, adopting the 5S methodology to drive their own improvements. Today, 5S is recognized globally as a fundamental aspect of lean manufacturing, providing a solid foundation for continuous improvement and operational excellence.
Benefits of 5S Training for Organizations
Implementing 5S training in your organization can yield a multitude of benefits, transforming your workplace into a model of efficiency and productivity. A significant advantage is the reduction of defects in production, directly impacting product quality and customer satisfaction. Minimizing waste and optimizing resource use can also lead to substantial environmental benefits.
A well-organized and clean work environment boosts productivity, safety, and employee morale. Employees are more likely to take pride in their workplace, leading to higher engagement and collaboration. This positive shift in workplace culture is further bolstered by management’s vocal support for 5S initiatives. When leaders champion these efforts, it fosters a sense of ownership and responsibility among team members in various work environments.
Start by listing some forbidden forms of the keyword “begin” according to the rule 5. Then, find out if there’s a chance to incorporate the keyword without making any extra assumptions, according to the rule 2. Keep it short. Before you begin, ensure you understand the requirements clearly.
The long-term benefits of 5S training are manifold. Creating more efficient and organized work areas helps organizations save time, money, and energy. This approach to workplace optimization leads to sustained improvements in operational efficiency and employee satisfaction. Moreover, the continuous improvement culture fostered by 5S training ensures that these gains are not fleeting but are maintained over time.
After:
The long-term benefits of 5S training include:
- More efficient and organized work areas, which help organizations save time, money, and energy.
- Sustained improvements in operational efficiency.
- Increased employee satisfaction.
- A continuous improvement culture that ensures gains are maintained over time.
Effective communication and support during the introduction of 5S are critical to its success. Providing informational materials and engaging employees through workshops and training sessions can help ease the transition and ensure everyone is on board. The free 5S workshop offered by Dmaic.com, for instance, is an excellent resource for enhancing efficiency and productivity in workplaces.
Key Components of Effective 5S Training
For 5S training to be effective, it must be thoughtfully designed and executed. One key component is the inclusion of interactive and practical activities, such as industry-specific case studies and simulations. These hands-on experiences facilitate learning and help employees understand how to apply 5S principles in their daily tasks.
Continuous training is another critical element. Regular refreshers and ongoing education ensure that the 5S principles remain relevant and top of mind for employees. Proper planning of the training program is essential to tailor it to the specific needs of your sector, making the lessons more applicable and impactful.
The availability of practical knowledge tools and resources, such as downloadable templates and action guides, can greatly enhance the effectiveness of a 5S training course. The Knowledge Academy, for example, offers a comprehensive course that covers the fundamentals of 5S, implementation techniques, and step-by-step guidance for achieving workplace organization and safety.
By incorporating these elements, you can ensure that your 5S training program is robust and effective.
Implementing Training on 5S in Your Workplace
Implementing 5S training in your workplace begins with careful preparation. Defining the program’s scope and objectives to align with your organization’s needs is the first step. Creating a timeline for implementation allows employees to gradually adapt to new expectations and ensures a smooth transition.
During the sorting phase, a red tag system can be utilized to identify items that may no longer be needed in the workspace. This helps in decluttering and organizing the work area more efficiently. Visual management tools, such as shadow boards, are also useful in ensuring that tools and materials are easily accessible and returned to their proper locations. Additionally, red tags can be used to mark these items for removal.
Implementing 5S in specific areas, such as warehouses, can lead to accurate stock management and reduced search times, further enhancing workplace efficiency. Sustaining these practices requires creating a schedule that integrates 5S tasks into regular operations. A feedback mechanism allows teams to suggest improvements and continually refine the 5S process.
Setting measurable goals is crucial to track the effectiveness of 5S implementation over time. Executing a comprehensive 5S training course helps build new habits that drive continuous improvement, efficiency, and productivity.
Practical Examples of 5S in Action
Seeing the 5S methodology in action can be incredibly inspiring and informative. In the cosmetics manufacturing industry, a standardized 5S process ensures workspace organization, cleanliness, and regular inspections, leading to higher product quality and safety. This systematic approach helps in maintaining a hygienic production space and smoother operations.
Implementing 5S in the beverage industry has reduced bottle breakage and cross-contamination, critical for maintaining consumer health. Organizing the workplace and ensuring regular cleaning helps these companies deliver safer, higher-quality products.
The electronics manufacturing industry also benefits greatly from 5S. Given the precision required in this field, maintaining an organized and clean work environment is essential for product safety. Regular cleaning and inspections promote a hygienic production space and minimize the risk of errors or defects.
Organizing the organized workspace in the textile industry helps workers locate key elements quickly, providing space for work and reducing injury risks.
Continuous Improvement with 5S
The 5S methodology serves as a robust foundation for fostering a culture of continuous improvement in organizations. Embedding new standards into the workplace culture ensures employees do not revert to old habits, maintaining the improvements achieved. This sustainability is crucial for long-term success and operational excellence.
Implementing 5S encourages employees to actively engage in identifying and solving workplace issues. This proactive approach minimizes hazards and encourages regular maintenance, leading to a safer work environment. Additionally, it helps minimize time and motion waste, fostering an efficient workflow.
The culture of continuous improvement promoted by 5S is not limited to the manufacturing floor. It extends to all areas of the organization, driving overall efficiency, safety, and productivity. Standardizing practices and sustaining the gains ensures organizations remain competitive and innovative in their industries.
Resources for Training on 5S
Finding the right resources for 5S training is essential for successful implementation. Gemba Academy offers a comprehensive 5S training series featuring over 2000 videos on Lean management and Six Sigma methodologies. These courses emphasize learning from expert practitioners who have significant real-world experience in implementing Lean principles.
Other notable resources include the 5S Methodology course conducted by a certified Six Sigma professional, which includes over 4 hours of video lectures. The 5S Concept Certified training course, created by MSI, is self-paced and offers lifetime access upon purchase.
For those looking for cost-effective options, ASQ offers a 30-minute 5S training course for $35, while the Alison 5S training course is free.
Summary
In conclusion, the 5S methodology is a powerful tool for enhancing workplace efficiency and fostering a culture of continuous improvement. By understanding the origins, benefits, and practical applications of 5S, organizations can transform their work environments and achieve operational excellence.
Implementing effective 5S training and utilizing the right resources will ensure that these principles are deeply embedded in your organization’s culture. Embrace the journey of continuous improvement and unlock the full potential of your workplace with 5S.
If you want to deepen your practical knowledge on how to effectively implement the 5S principles in your company, I invite you to join my training. You can sign up here
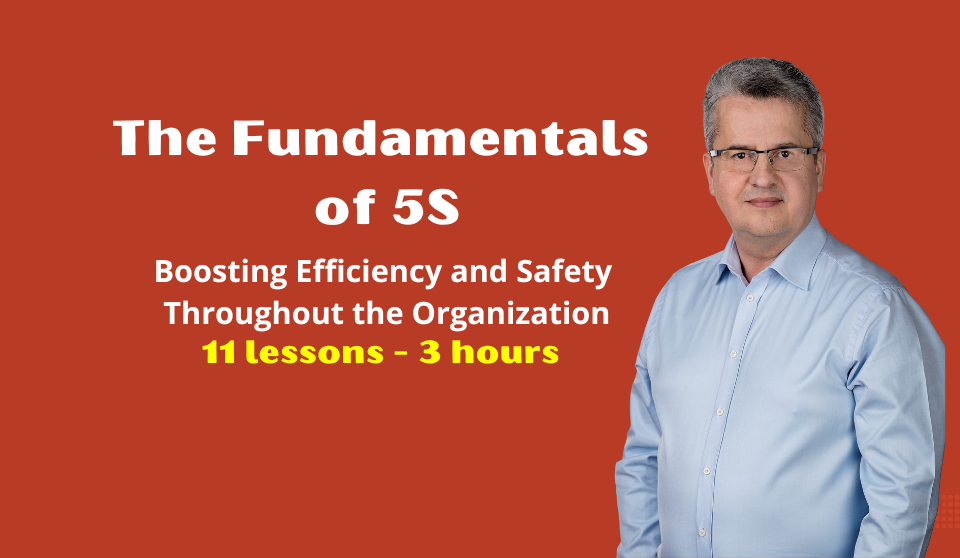
Practical training on 5S
Frequently Asked Questions
What are the five steps of the 5S methodology?
The five steps of the 5S methodology are Sort, Set in Order, Shine, Standardize, and Sustain. Each step contributes to fostering an organized and efficient work environment.
How did the 5S methodology originate?
The 5S methodology originated in Japan as a component of the Toyota Production System, significantly influenced by the works of Taiichi Ohno and Shigeo Shingo. This systematic approach emphasizes organization and efficiency in the workplace.
What are the benefits of 5S training for organizations?
5S training enhances workplace organization, efficiency, safety, and employee morale, while promoting a culture of continuous improvement and yielding long-term cost savings. Implementing this training can significantly benefit your organization’s operational effectiveness.
What are some key components of effective 5S training?
Effective 5S training is characterized by interactive activities, continuous education, and practical tools like audit checklists and action guides, all tailored to the organization’s specific needs. This approach ensures a more engaged and productive learning experience.
Where can I find resources for 5S training?
I’d like to invite you to my training session on how to effectively implement the 5S principles in your company. It’s a great opportunity to gain hands-on, practical knowledge. Sign up here: