Transform Your Organization with Effective Lean Games: Achieve Operational Excellence Through Simulation-Based Training
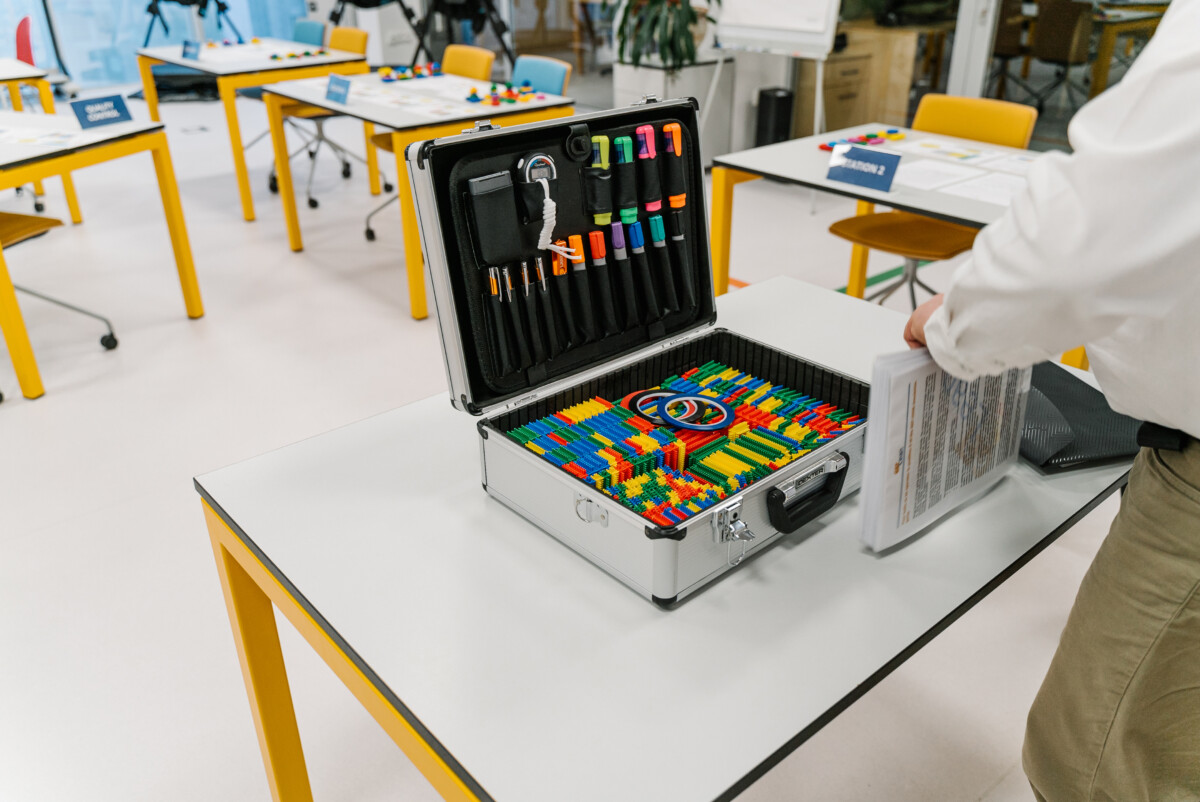
This portable training kit contains all materials needed to run effective lean games that boost engagement, teamwork, and Lean skills in any setting.
This portable training kit contains all the materials needed to run effective lean games that boost engagement, teamwork, and Lean skills within a company, enhancing organizational training and development.
Introduction
In today’s rapidly evolving business environment, companies are constantly looking for innovative methods to streamline operations, reduce waste, and foster a culture of continuous improvement. Simulation-based training through effective lean games is one of the most dynamic approaches to achieving these goals. These interactive training modules simplify complex Lean Manufacturing concepts and provide a practical, hands-on learning environment in which employees can experience real-world challenges and learn to overcome them.
Effective lean games create a controlled “laboratory” environment, allowing participants to experiment with process improvements risk-free. This experiential learning method has proven to be particularly engaging and transformative, enabling teams to identify inefficiencies and devise actionable solutions swiftly. Effective lean games help employees learn essential Lean principles and techniques, fostering best practices that enhance productivity and organizational efficiency. They empower organizations to drive measurable performance improvements by bridging the gap between theory and practice while instilling a mindset of collaboration and continuous growth.
Drawing upon my 25 years of experience implementing Lean Manufacturing principles across global industries, this article will explore how effective lean games can be an indispensable tool for modern businesses. We will delve into the core principles of Lean Manufacturing, examine how simulation-based training works, and show you exactly how these lean games can propel your organization towards operational excellence.
Throughout this article, we will cover:
- Understanding Lean Manufacturing: The foundational principles that drive efficiency and value.
- The Concept of Effective Lean Games: What makes these simulations stand out as a superior training tool.
- Mechanics of Our Simulation Tool: A detailed breakdown of how our effective lean games are structured and how they operate.
- Real-World Success Stories: Global references and testimonials that demonstrate the outstanding impact of these games.
- Business Benefits: How effective lean games improve productivity, enhance quality, and reduce operational costs.
- Implementation Guidelines: Best practices for integrating simulation-based training into your organization.
- A Special Offer for Customers: Exclusive bonus details that reward purchasers with complimentary course access.
By the end of this comprehensive guide, you will have a clear understanding of why effective lean games are critical for any organization seeking to instill Lean principles and drive sustainable improvements.
The Foundation: Understanding Lean Manufacturing
What is Lean Manufacturing?
Lean Manufacturing is a systematic approach that focuses on minimizing waste while maximizing value. Originating from the Toyota Production System, its core objective is to deliver exactly what the customer needs while using the fewest resources possible. This methodology centers on five core principles:
- Value: Define value from the perspective of the end customer.
- Value Stream: Identify and map every step involved in producing the product or service, highlighting non-value-added activities.
- Flow: Ensure that every stage of the process flows smoothly without interruptions.
- Pull: Produce only what is needed when it is needed, based on real customer demand.
- Continuous Improvement (Kaizen): Constantly seek ways to improve the process, striving for perfection even though it may never be fully reached.
These principles are designed to create efficient, responsive, and customer-centric operations. By eliminating waste (whether it be in the form of excess inventory, unnecessary movement, overproduction, or defects), Lean Manufacturing not only improves quality and productivity but also directly contributes to reducing operational costs.
Why Lean Manufacturing Matters
In a global economy where market demands are constantly changing, Lean Manufacturing helps organizations remain agile. Companies that adopt Lean strategies are better positioned to respond quickly to customer needs, manage production fluctuations, and sustain a competitive edge. Furthermore, Lean principles foster a culture of teamwork, accountability, and continuous improvement—qualities that are essential for long-term success.
Simulation-based training in the form of effective lean games reinforces these principles by offering an immersive and interactive way for employees to internalize them. Lean management tools, such as starter kits and training games, are designed to engage employees and develop their skills, fostering creativity and teamwork while ensuring cost-effective training that aligns with continuous improvement principles. By experiencing the challenges and rewards of Lean processes firsthand, participants gain a deeper, practical understanding that theoretical training alone cannot provide.
The Power of Effective Lean Games
What Are Effective Lean Games?
Effective lean games are simulation-based training modules designed to demonstrate the core principles of Lean Manufacturing in an interactive environment. Unlike basic free simulations, these games are structured with a focus on real-world application. They simulate complex production environments and include elements such as role assignments, time constraints, data tracking, and iterative feedback loops to mimic the challenges faced in actual manufacturing or service operations.
In the context of professional e-learning programs, educational games play a crucial role in enhancing group training. These games facilitate teamwork and problem-solving, allowing participants to engage collaboratively to achieve specific objectives during the training sessions. The objective of effective lean games is to create a realistic yet safe space where employees can experiment with process changes, experience the impact of their decisions, and witness measurable improvements. This method transforms abstract Lean concepts into concrete actions, enabling teams to see the direct benefits of streamlining processes, reducing waste, and improving overall efficiency.
Why Simulation-Based Training Works
Simulation-based training, and particularly effective lean games, offers several distinct advantages over traditional training methods. It is an excellent way to introduce new concepts or methodologies to teams, minimizing resistance and enhancing engagement:
- Immersive Learning: Participants actively engage in the simulation, making decisions and observing outcomes in real time. This hands-on experience leads to better knowledge retention and a deeper understanding of Lean principles.
- Safe to Fail: In a controlled simulation, mistakes are valuable learning experiences rather than costly errors. Employees can experiment with different strategies without risking actual business operations.
- Collaborative Environment: Lean games are designed to promote teamwork. Role assignments mimic real organizational structures, enabling cross-functional collaboration and communication that are essential in any Lean transformation.
- Immediate Feedback: The simulation environment provides real-time data on performance metrics such as cycle time, defect rates, and productivity. This immediate feedback loop allows for rapid adjustments and continuous improvement.
- Bridging the Gap Between Theory and Practice: By applying Lean principles in a simulated environment, participants can see how theoretical ideas work in practice. This experiential learning ensures that lessons learned during the simulation are readily applicable in the workplace.
The Difference Between Free Lean Games and Effective Lean Games
While there are many free lean games available online, they typically offer only a rudimentary introduction to Lean concepts. Effective lean games, on the other hand, are designed to be comprehensive and adaptable to real-world operational complexities. Here are some key differences:
- Depth of Learning: Free lean games might only cover basic aspects of Lean Manufacturing, whereas effective lean games provide an in-depth look into advanced Lean methodologies.
- Data-Driven Feedback: Effective lean games come with robust mechanisms for performance tracking and detailed analysis, enabling teams to quantify improvements and understand the impact of their actions.
- Customization and Adaptability: Our simulation tool, built on decades of experience, can be tailored to mirror the unique challenges of a given organization. This ensures that each training session is relevant and actionable.
- Comprehensive Facilitation: Effective lean games are typically supported by facilitator guides, structured debrief sessions, and additional resources that help bridge the gap between simulation exercises and real-world application.
- Clear Instructions: Effective lean games come with detailed instructions that provide clear, organized guidance for various Lean games and training activities. This ensures all participants understand the concepts being taught, thereby enhancing overall productivity and engagement during training sessions.
The enhanced learning potential of effective lean games makes them a more valuable investment for organizations looking to achieve lasting improvements.
Mechanics and Structure of Our Simulation Tool
From Free Lean Games to a Licensed Simulation Tool
Based on over 25 years of practical experience in implementing Lean Manufacturing across various industries, our simulation tool has evolved from simple, free lean games into a robust, licensed product. Developed through years of refinement and field testing with companies such as General Motors, Gillette, Timken, and ABB, our simulation tool is a product of deep expertise and real-world insights. Initially, it was introduced as a pilot program to test and optimize its features before a full-scale rollout, ensuring it could effectively refine training methods and increase productivity.
Our licensed simulation tool is not just a game—it is an interactive learning environment that blends theoretical principles with practical applications. It is designed to challenge participants, offer detailed metrics, and encourage teamwork, all while providing a realistic portrayal of production processes and Lean challenges.
The Simulation Process: A Step-by-Step Guide
Our simulation tool unfolds over four rounds, each designed to build upon the previous one and drive continuous improvement. Here is an overview of how an effective lean game session is structured:
- Preparation and Role AssignmentThe facilitator begins by setting up the training environment to reflect a real production floor. Workstations are arranged strategically, and all necessary materials—such as physical tokens representing inventory items—are prepared. Each participant is assigned a specific role, such as operator, quality inspector, material handler, or manager, along with a detailed instruction sheet. This stage lays the foundation for the session by ensuring that every participant understands their responsibilities.
- Baseline Production RoundThe first round is conducted without any Lean interventions. Participants follow their usual processes, resulting in high levels of waste, delay, and errors. This intentional chaos serves to illustrate the inefficiencies present in unstructured systems. Key performance indicators, including production throughput, defect rates, and cycle times, are recorded to establish a performance baseline.
- Data Collection and DebriefAfter the baseline round, the facilitator collects detailed data and conducts a debriefing session. Participants analyze the results, identifying the key sources of waste and inefficiencies. This reflection is critical, as it sets the stage for the introduction of Lean practices in subsequent rounds.
- Introduction of Lean ToolsIn the following rounds, specific Lean tools such as Kanban, 5S, and one-piece flow are introduced. Teams reconfigure their work processes to incorporate these tools. For example, they may reorganize their workstations to minimize unnecessary movement or implement a Kanban system to regulate inventory levels. This phase demonstrates how systematic changes lead to improvements in production efficiency.
- Iterative Rounds and Continuous ImprovementThe simulation continues through multiple rounds, with each session building on the improvements observed in the previous one. Data collection and analysis are repeated, providing a clear picture of progress over time. This iterative approach reinforces the PDCA (Plan-Do-Check-Act) cycle, a cornerstone of Lean Manufacturing, and helps participants understand that continuous improvement is an ongoing process.
- Final Review and Action PlanningAt the conclusion of the simulation, a final assessment is conducted. The team reviews all the collected data, discusses successes and areas for further improvement, and develops an action plan for implementing these lessons in their real-world operations. This final review solidifies the learning experience and ensures that insights gained during the session are not lost but are transformed into practical strategies for long-term improvement.
For a detailed game description and a comprehensive overview of our simulation tool, please click the internal link provided. Additionally, if you are ready to invest in a transformative training experience, you can also purchase the simulation tool directly from our website.
Real-World Impact: Global Success Stories of Effective Lean Games
Testimonials from Diverse Industries
Effective lean games have proven to be a powerful catalyst for change in organizations across the globe. Numerous companies, both large and small, have harnessed the power of simulation-based training to drive operational improvements and cultivate a culture of continuous improvement. These games help employees learn essential Lean principles and techniques, fostering best practices that enhance productivity and organizational efficiency. Here are some examples of how global organizations have benefited:
- Automotive Industry: Leading manufacturers in Europe and North America have reported significant reductions in production cycle times and waste after integrating our simulation tool into their training programs. For instance, several automotive suppliers have experienced up to a 50% decrease in lead times and substantial improvements in quality control.
- Healthcare Providers: Hospitals and healthcare networks have successfully applied Lean principles learned through effective lean games to streamline patient care processes, reduce waiting times, and improve service delivery. The result is a more efficient workflow that enhances patient satisfaction and staff morale.
- Large-Scale Manufacturers: Renowned multinational companies have leveraged simulation-based training to identify and eliminate production bottlenecks. These improvements have translated into measurable cost savings and higher operational efficiency, reinforcing the impact of effective lean games.
- Educational Institutions: Universities and business schools incorporate effective lean games into their curricula, offering students a hands-on opportunity to bridge the gap between theory and practice. This experiential approach enhances learning outcomes and prepares future managers for real-world challenges.
Global References and Industry Recognition
Our simulation tool is not an isolated concept; it is backed by decades of experience and has been successfully implemented by many organizations worldwide. Global industry leaders and renowned organizations such as General Motors, Gillette, Timken, and ABB have all contributed to the evolution of our simulation-based training. These references serve as a testament to the effectiveness of our approach and underline the valuable insights gleaned from practical Lean Manufacturing implementation.
Through effective lean games, participants witness firsthand the benefits of structured process improvements, such as reduced defects, improved cycle times, and lower overall operational costs. These success stories emphasize that simulation-based training is not merely an academic exercise but a proven strategy for achieving real business transformation. By incorporating lean management principles, our training fosters a culture of teamwork and continuous improvement, ensuring that employees are engaged and equipped with the skills necessary for sustained success.
Business Benefits of Effective Lean Games
Driving Productivity and Operational Efficiency
One of the most significant benefits of effective lean games is the direct impact on productivity. By engaging in simulation-based training, teams learn how to identify and eliminate waste, thereby streamlining their operations. The emphasis on process optimization, real-time decision-making, and continuous improvement leads to higher throughput and more efficient resource utilization.
Through multiple iterations of Lean games and simulations, employees gain a better understanding of how minor adjustments in their workflows can lead to major improvements in performance. This practical insight results in reduced lead times and a leaner, more agile organization capable of adapting quickly to market changes.
Enhancing Quality and Reducing Waste
Quality is the foundation of any successful manufacturing process. Effective lean games enable participants to address quality issues directly by simulating production scenarios where defects and errors are immediately apparent. This real-time exposure to quality challenges compels teams to implement proactive measures such as error-proofing, standardized work practices, and robust quality controls.
Lean games also emphasize waste elimination by allowing employees to practice Lean principles in real-world scenarios. These interactive simulations help teams identify and eliminate waste, optimize processes, and enhance operational efficiency. As effective lean games teach teams to manage and monitor quality metrics, organizations experience a decrease in waste and rework. The outcome is a more consistent product quality that translates to improved customer satisfaction and a stronger competitive position in the market.
Cultivating a Culture of Continuous Improvement
At the heart of Lean Manufacturing is the philosophy of continuous improvement—or Kaizen. Effective lean training and games embed this mindset by allowing employees to experiment with process changes and witness the impact of their decisions immediately. This practical and immersive approach encourages every team member to take ownership of the improvement process and promotes a culture where regular, incremental enhancements become the norm.
A culture of continuous improvement has far-reaching benefits. It not only drives operational excellence but also fosters innovation, improves employee morale, and helps the organization stay ahead in a competitive marketplace.
Facilitating Better Communication and Teamwork
Effective lean games require participants to collaborate closely while assuming various roles within the simulation. By playing interactive games that engage teams with Lean principles, participants can enjoy learning and grasp complex methodologies without the stress of conventional training methods. This cross-functional team experience enhances communication and breaks down traditional departmental silos. By working together to overcome operational challenges, team members learn to appreciate different perspectives and develop a shared vision for improvement.
Improved communication and teamwork are key to sustaining long-term process improvements. When employees trust each other and work together effectively, the entire organization benefits from faster problem resolution, greater innovation, and a more harmonious work environment.
Implementing Effective Lean Games: Best Practices
Planning and Preparing for a Successful Session
Before implementing effective lean games as part of your training program, thorough planning is essential. Begin by setting clear objectives and identifying specific areas in your operations where you would like to see improvement. Consider starting with a pilot program to test the initial phases of your project. This allows you to optimize processes, refine training methods, and ensure increased productivity before a full-scale rollout. Establish baseline metrics such as defect rates, cycle times, and inventory levels to measure progress throughout the simulation.
Ensure that the training environment is prepared to replicate a realistic production setting. Arrange workstations in a manner that mirrors the actual layout of your operations, and organize all necessary materials—including tokens, role cards, and data collection tools—in advance. This attention to detail will help participants immerse themselves fully in the simulation.
Selecting the Right Participants
Effective lean games are most successful when the training session includes a diverse group of participants from different departments, including frontline operators, quality control personnel, material handlers, and managers. In e-learning training, it is crucial to designate one person as the trainer during the activities, highlighting the importance of individual contributions in collaborative learning environments. This cross-functional representation ensures that every aspect of the production process is addressed, and it encourages a holistic approach to problem-solving. Involving the right mix of employees fosters a richer learning environment and helps ensure that insights from the simulation can be effectively implemented across the organization.
Conducting Structured Debrief Sessions
A critical component of effective lean games is the debrief session that follows each simulation round. In these sessions, the facilitator guides participants through a detailed review of the data collected during the simulation. Activities that require participants to draw or illustrate concepts, such as the ‘Standard Pig’ exercise where everyone is instructed to draw a pig following specific guidelines, can be particularly effective. Encourage open discussion about what worked, what didn’t, and what could be improved. This reflective process not only reinforces key Lean concepts but also provides actionable insights that can be implemented in the real world.
Structured debrief sessions are essential for transforming simulation experiences into lasting operational changes. They help participants understand the correlation between their actions in the game and the outcomes in a real production environment, ensuring that the learning is both deep and practical.
Iterative Improvement and Continuous Feedback
Effective lean games are not a one-time exercise—they are part of an ongoing process of continuous improvement. Lean games and simulations often involve multiple iterations, allowing participants to re-run or repeat the exercises several times. After each simulation round, use the insights gained to adjust strategies, implement additional Lean tools, and iterate on the process. This iterative cycle reinforces the PDCA (Plan-Do-Check-Act) model, ensuring that every change is evaluated, fine-tuned, and built upon in subsequent rounds.
Establish mechanisms for continuous feedback throughout the simulation process. Real-time data collection and analysis enable teams to see the direct impact of their improvements and encourage them to keep pushing for better performance.
The Role of Gamification in Effective Lean Games
Engaging and Motivating Employees
One of the key differentiators of effective lean games is their incorporation of gamification elements. Playing interactive games transforms learning into an engaging, competitive, and fun experience. By introducing game-like challenges, rewards, and team-based competition, employees are more likely to remain motivated and invested in the training process.
The competitive yet collaborative environment inherent in effective lean games not only drives individual engagement but also enhances overall team dynamics. When employees compete to achieve better performance metrics and share best practices during debrief sessions, the entire organization benefits from a heightened level of enthusiasm and commitment to continuous improvement.
Realizing the Benefits of Simulation-Based Training
Simulation-based training leverages the power of gamification to create a dynamic learning environment. Effective lean games, often referred to as training games, provide a platform where theoretical Lean principles are not just taught but actively experienced. These innovative educational tools are designed to teach Lean principles and promote teamwork among employees. The immediacy of feedback and the iterative nature of the simulation allow participants to experiment with different strategies and see tangible results almost immediately.
The strategic use of gamification in training helps bridge the gap between classroom learning and operational execution. When employees are engaged in an interactive simulation, they are more likely to embrace the Lean mindset and apply these principles in their daily work. This is the ultimate advantage of effective lean games: they turn abstract theories into actionable strategies that drive real business results.
For more insights on the benefits of gamification, you can explore this external resource on the benefits of gamification. And to understand the advantages of simulation-based process improvement training, refer to this external resource on simulation training benefits.
Driving Business Transformation Through Effective Lean Games
Bridging the Gap Between Strategy and Execution
Effective lean games are designed to translate strategic Lean Manufacturing principles into executable practices. By simulating various production scenarios, these games allow teams to see how even minor adjustments in process design can lead to significant improvements in efficiency and quality. This hands-on experience is invaluable in bridging the gap between high-level strategy and the detailed execution required on the shop floor. By incorporating systems thinking, teams can better understand their dynamics and overall workflow optimization, recognizing the importance of their operations as an interconnected whole rather than just focusing on individual components.
The data collected during each simulation round provides a clear picture of the impact of Lean interventions. Organizations can use this data to make informed decisions, adjust workflows, and implement process changes that drive competitive advantage. By integrating effective lean games into your training regimen, you empower your team to put strategy into action and achieve measurable operational improvements.
Improving Customer Satisfaction and Reducing Costs
At the heart of Lean Manufacturing is the goal of delivering greater value to the customer. Effective lean games demonstrate how improvements in operational efficiency lead to faster production cycles, fewer defects, and ultimately, higher-quality products. These interactive simulations allow employees to practice Lean principles like waste elimination and process optimization in real-world scenarios. When these improvements are translated into real-world performance, the result is increased customer satisfaction and a stronger market reputation.
Cost reduction is another significant benefit of effective lean games. By systematically identifying and eliminating waste, organizations can reduce production costs, minimize rework, and improve resource utilization. The cumulative effect of these improvements is a leaner, more cost-effective operation that is well positioned to meet market demands.
Cultivating a Culture of Innovation and Continuous Improvement
Effective lean games are not just about operational metrics—they also play a crucial role in fostering a mindset of innovation and continuous improvement. Lean training, with its practical and immersive approaches, allows employees to apply theoretical concepts in real-world scenarios. As employees engage with the simulation, they learn to think critically, experiment with new ideas, and collaborate to solve complex problems. This culture of constant learning and improvement is essential for sustaining long-term success in today’s competitive business landscape.
By instilling a spirit of continuous improvement, effective lean games help organizations evolve beyond mere process optimization. They create an environment where every employee is empowered to contribute to the company’s growth, driving innovation across all levels of the organization.
Integrating Effective Lean Games into Your Training Program
Strategic Planning and Rollout
Successful integration of effective lean games into your company begins with strategic planning. Identify key areas in your operations where improvements are most needed and set specific, measurable objectives. Develop a clear roadmap that outlines how simulation-based training will be incorporated into your broader Lean strategy to benefit the company and its employees.
Preparation is key—ensure that all training materials, including role cards, tokens, and data collection tools, are ready before the session. Create a training schedule that allows for multiple simulation rounds with regular intervals for feedback and debriefing. This strategic planning ensures that the benefits of effective lean games are fully realized and translated into real-world improvements.
Customizing the Experience for Your Organization
Every organization faces unique challenges, and a one-size-fits-all approach rarely delivers optimal results. Our simulation tool is designed to be highly customizable, allowing you to tailor the scenarios and role assignments to match the specific nuances of your operational environment. In the context of e-learning training, each person can take on significant roles within group exercises. For instance, one person may be designated as a trainer during the training activities, showcasing the importance of individual contributions in collaborative learning environments. Whether you are running a manufacturing plant, a service center, or a distribution hub, effective lean games can be adapted to mirror your specific processes and challenges.
Customization not only enhances the relevance of the simulation but also ensures that the insights gained during the training are directly applicable to your operations. This tailored approach makes effective lean games a powerful tool for driving targeted improvements and achieving sustainable success.
Leadership Involvement and Ongoing Support
For effective lean games to drive transformation, active leadership involvement is essential. When managers and executives participate in the simulation, they signal their commitment to continuous improvement. Activities that require participants to draw or illustrate concepts, such as the ‘Standard Pig’ exercise where everyone is instructed to draw a pig following specific guidelines, can be particularly effective. This leadership engagement fosters a culture of accountability and motivates employees to embrace Lean principles.
Ongoing support is also critical. After each simulation session, follow up with additional training, coaching sessions, or targeted projects to ensure that the lessons learned are implemented effectively. This continuous reinforcement of Lean practices helps embed the improvement process into the fabric of your organization.
A Special Bonus for Our Valued Clients
As a token of appreciation for investing in our advanced simulation tool—built on decades of practical Lean Manufacturing expertise—we are excited to offer an exclusive bonus for every purchaser. All organizations that invest in our simulation tool will receive an email containing a special code, granting free access to all courses available on our site. This bonus is designed to further support your Lean journey by providing additional learning resources and ongoing training opportunities.
Final Thoughts: Embrace Effective Lean Games for Operational Excellence
Effective lean games offer a transformative approach to training that goes far beyond traditional methods. By immersing employees in realistic, hands-on simulations, these games not only teach the fundamentals of Lean Manufacturing but also empower teams to drive meaningful improvements in their everyday operations.
Drawing upon over 25 years of hands-on experience implementing Lean principles in companies such as General Motors, Gillette, Timken, and ABB, our simulation tool represents the pinnacle of what effective lean games can offer. It is a comprehensive, data-driven solution that bridges the gap between theory and practice, ensuring that every lesson learned translates into tangible, measurable benefits for your organization.
Whether your goal is to reduce waste, enhance quality, lower operational costs, or foster a culture of continuous improvement, effective lean games provide the ideal platform to achieve these objectives. By incorporating lean management principles, these games foster creativity and teamwork, ensuring cost-effective training that aligns with continuous improvement principles.
For a more detailed game description and comprehensive insights into how our simulation tool works, please visit our dedicated page. If you’re ready to revolutionize your training and transform your operations, you can purchase the simulation tool today.
Recap: Why Effective Lean Games Are Essential
Immersive Learning: Effective lean games, including innovative training games, create an engaging, safe, and realistic environment where employees can experiment and learn by doing.
Bridging Theory and Practice: By simulating complex production scenarios, these games allow teams to apply Lean Manufacturing principles in a context that mirrors real-world challenges.
Data-Driven Improvement: With robust metrics and iterative feedback, effective lean games provide clear insights into process inefficiencies and measurable performance gains.
Enhanced Team Collaboration: The role-based structure of the simulation fosters cross-functional communication and teamwork, which are crucial for sustained Lean transformation.
Sustainable Business Benefits: From reduced lead times and lower costs to improved product quality and higher customer satisfaction, effective lean games deliver substantial, quantifiable benefits.
Tailored for Your Needs: Our simulation tool can be customized to address the specific challenges of your organization, ensuring that the training is both relevant and impactful.
By integrating these powerful training tools into your organization, you not only drive operational excellence but also create a foundation for continuous, data-driven improvement that can help you stay ahead in today’s competitive business landscape.
Conclusion
In conclusion, effective lean games are much more than just fun, interactive training modules—they are a strategic asset for organizations striving for operational excellence. By immersing employees in simulation-based training, these games transform Lean Manufacturing theories into practical, actionable improvements that deliver lasting results. Lean training, with its practical and immersive approaches, enhances creativity, fosters collaboration, and promotes a culture of continuous improvement within organizations. With proven success across industries and a global track record, our simulation tool stands as a testament to the power of effective lean games in driving continuous improvement.
Investing in our simulation tool, refined over 25 years through real-world experience with industry giants such as General Motors, Gillette, Timken, and ABB, is a strategic decision that can revolutionize your training programs and operational processes. Empower your workforce, improve productivity, and foster a culture of innovation with a training solution that brings Lean Manufacturing to life.
For further insights and to experience a transformative learning journey, visit our detailed game description. Ready to take the leap? You can also purchase the simulation tool now and unlock an exclusive bonus: an email with a special code granting free access to all courses available on our site.
Harness the power of effective lean games today and drive your organization toward a future of sustained excellence and continuous improvement.