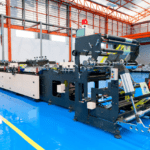
Understanding SMED: Streamlining Your Processes
February 9, 2025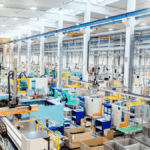
Lean Productivity Tips to Work Smarter and Faster
April 23, 2025Want to boost efficiency and quality in your manufacturing processes? This guide on process improvement in manufacturing covers key techniques like Lean, Six Sigma, and Kaizen. Learn how these methods can eliminate waste, reduce defects, and streamline workflows. Read on to discover actionable steps to optimize your operations.
Key Takeaways
- Process improvement in manufacturing enhances performance, efficiency, and profitability, allowing organizations to maintain a competitive edge in the market.
- Key techniques for process improvement include Lean manufacturing, Six Sigma, Kaizen, and Total Quality Management, each providing unique methods to eliminate waste and enhance quality.
- Sustaining a culture of continuous improvement requires employee engagement, effective communication, and leadership commitment to foster ongoing operational excellence.
Importance of Process Improvement in Manufacturing
In the manufacturing industry, process improvement is vital for enhancing performance, efficiency, and profitability. Faster production, cost reduction, and improved product quality help manufacturers remain competitive in an ever-evolving market. Continuous improvement leads to better quality, lower costs, and a significant competitive edge.
Efficient methodologies enable companies to anticipate future challenges and adapt to market requirements, thereby maintaining their competitive edge. This proactive approach enables organizations to optimize productivity and profitability by refining their internal processes and procedures. Improved transparency in process visibility allows stakeholders to track progress and make data-driven decisions—for instance, better detection of bottlenecks led to improved decision-making in a food processing plant.
Moreover, fostering effective communication through daily meetings can help resolve production problems quickly, enhancing workplace safety and reducing accidents. Automation also plays a crucial role by minimizing human error and allowing employees to focus on higher-value tasks. A conservative mindset and reliance on outdated processes can hinder process improvement, but recognizing and refining unnecessary or redundant practices can lead to significant operational improvements.
Top Techniques for Process Improvement in Manufacturing
Process improvement techniques are designed to enhance efficiency and productivity in manufacturing operations while minimizing waste and identifying areas for improvement. This process improvement technique, along with other process improvement methods, focuses on enhancing overall performance.
Some of the most significant techniques used in the industry include:
- Lean manufacturing
- Kanban
- Six Sigma
- Kaizen
- Total Quality Management
These methodologies provide a comprehensive toolkit for refining processes and achieving operational excellence.
Organizations implement various business process improvement methodologies to adapt their processes effectively to customer demands. Interestingly, combining different techniques can often yield better results, as each method brings unique strengths to the table. For example, Poka-yoke techniques are employed to prevent errors or defects, thereby enhancing overall quality.
Continuous flow in manufacturing also plays a critical role by arranging production processes in a smooth, uninterrupted sequence, which helps reduce lead times and minimize work-in-process inventory on the assembly line.
In the following sections, we will delve into the specifics of each top technique for process improvement in manufacturing. Each methodology offers distinct advantages and tools that can be tailored to meet the unique needs of your production processes. Whether you aim to eliminate waste, reduce defects, or streamline workflows, these techniques provide a solid foundation for continuous improvement.
Six Sigma Methodology
Six Sigma methodology is renowned for its focus on reducing process variation and defects in manufacturing. Its primary goal is to achieve a defect rate of fewer than 3.4 defects per million opportunities. Lean Six Sigma combines elements of Six Sigma and Lean Manufacturing to enhance process efficiency further by removing waste.
The DMAIC cycle, which stands for:
- Define
- Measure
- Analyze
- Improve
- Control
is a structured approach used to improve and standardize existing processes, thereby reducing process variation.
For developing new processes, the DMADV cycle—Define, Measure, Analyze, Design, and Verify—is employed.
Tools like the Fishbone diagram, also known as the Ishikawa diagram, and SIPOC analysis diagrams are commonly used during the analysis stage of the DMAIC process to brainstorm potential causes of defects and define processes by identifying Suppliers, Inputs, Processes, Outputs, and Customers.
By applying Six Sigma, manufacturers can see significant improvements in product quality, such as reducing air bubbles in glass products. Ultimately, Six Sigma aims to streamline workflows, standardize processes, and eliminate defects, all contributing to operational excellence and customer satisfaction.
Lean Manufacturing Principles
Lean Manufacturing, also known as Lean Production, was significantly developed by Toyota in the 1930s and ‘40s. The main goal is to remove waste, increase profits, and achieve efficient outputs. Lean methodology focuses on eliminating waste to maximize added value, identifying seven types of waste: transport, motion, waiting, over-processing, overproduction, defects, and excess inventory.
Lean production systems focus on creating a seamless and efficient flow of materials and information. Their goal is to minimize waste while maximizing customer value. Techniques like value stream maps analyze material and information flow, while lean manufacturing focuses on the Single Minute Exchange of Dies (SMED) to reduce changeover time for equipment setup.
Focusing on eliminating non-value-adding activities, Lean Manufacturing helps save time and costs while improving quality. This approach leads to operational excellence and better quality management across manufacturing operations.
Kaizen for Continuous Improvement
Kaizen, meaning ‘change for the better,’ is a philosophy that guides the continuous improvement model. It promotes small, incremental changes that engage all employees in the continuous improvement process, enhancing production processes through the use of lean techniques. The primary goal of Kaizen is to promote progressive improvement that involves every employee, ensuring that constant improvement is a collective effort.
Kaizen encourages employees to contribute ideas and actively participate in improvement initiatives, boosting productivity and streamlining workflows. This philosophy aligns with methods like Total Quality Management and Lean Manufacturing, focusing on customer satisfaction and operational excellence.
By continually improving processes, Kaizen enables organizations to maintain a culture of continuous improvement and enhanced quality management.
Total Quality Management (TQM)
Total Quality Management (TQM) is a comprehensive approach that focuses on creating an organization-wide culture of quality. The primary goal of TQM is to improve processes, enhance customer satisfaction, and foster effectiveness and competitiveness. TQM emphasizes continuous improvement across all levels of the organization to optimize processes and achieve better outcomes.
Effective communication and employee engagement are key to TQM in determining quality levels and driving improvements. This approach of TQM relies heavily on just-in-time manufacturing and Six Sigma principles, aiming to eliminate defects and enhance overall efficiency.
By fostering a culture of quality control and continuous improvement, TQM helps organizations produce high-quality products and maintain customer satisfaction.
Business Process Management (BPM)
Business Process Management (BPM) involves analyzing and improving business processes to ensure they align with current business objectives. The five main steps of BPM are Analyze, Model, Implement, Monitor, and Optimize. During the analysis step, current processes are mapped from start to finish, while the Modeling step involves drafting desired process improvements.
The Implementation step puts the model into action and establishes success metrics. In the Monitor step, these metrics are assessed to determine improvement. Finally, the Optimize step involves continuously identifying and addressing process inefficiencies.
Business process mapping is a valuable tool for visualizing the entire business process. It clarifies roles, responsibilities, and goals within the organization. By following these steps, BPM ensures continuous process improvement and operational excellence.
5S Methodology
The primary focus of the 5S methodology is on workplace organization and standardization, aiming to minimize waste, improve workflow, and eliminate non-value-adding processes. The 5S method includes five steps: Sort, Set in Order, Shine, Standardize, and Sustain.
According to the 5S methodology, an organized and clean environment is essential. It also emphasizes the importance of standardization as the foundation for many lean tools. By implementing the 5S method, manufacturers can create a more efficient and safe workplace, resulting in improved process efficiency and enhanced quality management.
The 5S methodology aligns with techniques like Six Sigma and Lean Manufacturing, contributing to continuous improvement and operational excellence.
Just-in-Time (JIT) Manufacturing
Just-in-Time (JIT) manufacturing emphasizes producing items only as needed to meet customer demand, reducing excess inventory and waste. Producing the right parts at the right time in the right quantities is the core principle of JIT. By meeting demand without excess inventory, JIT manufacturing helps streamline workflows and reduce defects.
This approach is closely aligned with the principles of Lean Manufacturing and the Toyota Production System, focusing on maximizing productivity and quality management. JIT manufacturing ensures that the entire production process is efficient and responsive to customer demand, leading to improved quality and operational excellence.
Root Cause Analysis
Root cause analysis in manufacturing identifies underlying causes of issues to prevent their recurrence. The 5 Whys Analysis technique is employed in root cause analysis to determine the underlying source of a problem within an organization.
Addressing root causes allows manufacturers to implement lasting solutions, improving process efficiency and product quality. Root cause analysis complements other methods by ensuring problems are effectively resolved, leading to continuous improvement and operational excellence.
Agile Methodology in Manufacturing
Agile methodology enhances manufacturing flexibility by facilitating rapid responses to market changes. This approach enables manufacturers to adapt quickly to evolving customer demands and market conditions, ensuring that their processes remain efficient and competitive.
The Agile methodology aligns with techniques such as Lean Manufacturing and Six Sigma, focusing on continuous improvement and operational excellence. Incorporating Agile principles helps streamline workflows, eliminate defects, and maximize productivity. This methodology ensures that manufacturing operations are responsive and adaptable, leading to improved quality and customer satisfaction.
Kanban System
The Kanban system is a visual workflow technique that helps eliminate bottlenecks and improve efficiency. It regulates the flow of materials and information to enhance process efficiency. A Kanban board is used for tracking progress, identifying problems, and improving efficiencies in manufacturing.
The Kanban system helps maintain optimal inventory levels and prevents overproduction, contributing to just-in-time production. This approach aligns with Lean Manufacturing and Total Quality Management principles, ensuring continuous process improvement and operational excellence. By implementing the Kanban system, manufacturers can streamline workflows, eliminate defects, and maximize productivity.
Implementing Digital Tools for Process Improvement
Digital tools play a crucial role in enhancing process improvement efforts in the manufacturing industry. Real-time data analytics allows for immediate adjustments to processes based on current performance, ensuring that operations remain efficient and responsive. Automation in manufacturing reduces manual error rates, enhancing overall process reliability.
Dashboards can track key performance indicators, making it easier to monitor progress over time, while digital tools can visualize workflows to identify bottlenecks and inefficiencies. Leveraging digital tools allows manufacturers to achieve continuous improvement, streamline workflows, and optimize production processes. This approach aligns with other methodologies, ensuring operational excellence and improved quality management.
Employee Engagement and Training
Engaged employees are crucial to continuous improvement, as they actively contribute ideas and participate in initiatives. Empowered employees are more proactive in identifying issues and suggesting viable solutions within their work processes. Regular training of employees and development opportunities are essential for maintaining a workforce that is committed to ongoing improvement.
Training in methodologies such as Lean and Six Sigma equips employees with the essential skills necessary for process optimization and improvement. Recognizing and rewarding contributions encourages engagement and motivation.
Continuous improvement initiatives benefit from structured recognition programs acknowledging employee contributions. Fostering a culture of engagement and training enables manufacturers to achieve operational excellence and drive continuous improvement.
Measuring and Tracking Process Improvement Efforts
Key performance indicators (KPIs) are essential measures used to evaluate the effectiveness of process improvement initiatives against predetermined targets.
KPIs can be categorized into:
- Strategic metrics
- Operational metrics
- Functional metrics
- Leading/lagging metrics
Each category provides insights at different organizational levels.
Process performance metrics specifically assess operational capabilities, helping to identify areas that require enhancements or adjustments for future process improvements.
Regularly reviewing KPIs ensures they remain relevant and aligned with the business’s evolving goals. Analytics software is often utilized to track and report on KPIs, enabling organizations to make informed decisions based on data.
Measuring and tracking efforts ensure continuous process improvement and operational excellence for manufacturers.
Sustaining a Continuous Improvement Culture
Sustaining a culture of continuous improvement is essential for maintaining relevance and efficiency as organizations grow and evolve. High employee engagement levels often lead to enhanced job satisfaction and reduced turnover. Regular feedback mechanisms enable employees to refine their contributions, driving further engagement in improvement efforts. Open communication channels help to foster a culture where employees can share ideas and feedback effectively.
Creating cross-functional teams fosters collaboration and utilizes diverse perspectives to enhance continuous improvement initiatives. Leadership commitment is critical to sustaining improvement efforts; when leaders leave, initiatives can falter.
A continuous improvement culture thrives when employees feel empowered to take the initiative and suggest enhancements. Building a strong culture of constant improvement helps organizations achieve sustained operational excellence and a competitive advantage.
Summary
In summary, process improvement in manufacturing is essential for enhancing efficiency, reducing costs, improving product quality, and maintaining a competitive edge. Techniques like Six Sigma, Lean Manufacturing, Kaizen, TQM, BPM, the 5S methodology, JIT manufacturing, Root Cause Analysis, Agile methodology, and the Kanban system each offer unique tools and strategies to achieve these goals. By integrating these methodologies, manufacturers can create a robust framework for continuous improvement and operational excellence.
Ultimately, the key to success lies in adopting a culture of continuous improvement, supported by engaged employees, practical training, and the implementation of digital tools. Measuring and tracking process improvement efforts through KPIs ensures that the initiatives remain aligned with organizational goals. As manufacturers strive for excellence, these process improvement techniques will serve as valuable guides on their journey to sustained success and innovation.
Frequently Asked Questions
What is the primary goal of Six Sigma methodology in manufacturing?
The primary goal of the Six Sigma methodology in manufacturing is to minimize process variation and defects, aiming for a defect rate of fewer than 3.4 defects per million opportunities. This focus significantly enhances product quality and operational efficiency.
How does Lean Manufacturing aim to improve production processes?
Lean Manufacturing aims to optimize production processes by eliminating waste, thereby maximizing added value and enhancing efficiency. By identifying seven types of waste and employing tools such as value stream mapping and SMED, workflows are streamlined, and overall quality is improved.
What is the philosophy behind Kaizen in manufacturing?
The philosophy behind Kaizen in manufacturing emphasizes continuous improvement through small, incremental changes that involve all employees. This approach fosters engagement and enhances production processes by utilizing lean techniques.
Why is employee engagement critical in process improvement efforts?
Employee engagement is crucial in process improvement efforts as it fosters active participation from employees who can contribute valuable ideas and solutions. This involvement not only drives continuous improvement but also enhances overall operational excellence.
What role do digital tools play in process improvement?
Digital tools are instrumental in process improvement by delivering real-time data analytics, automating tasks to minimize errors, and visualizing workflows to pinpoint inefficiencies. Consequently, they facilitate continuous improvement and operational excellence.